Special Report: Comet, Maquire, Una-Dyn provide alternative drying methods
Desiccant dryers might produce the biggest sales numbers, but buyers have other options, too.
For example, Universal Dynamics Inc., Comet Plastic Equipment LLC and Maguire Products Inc. recently introduced new dryers that employ other technologies. Una-Dyn's new model combines desiccant drying with what it calls "reactor drying technology," Comet's relies on compressed air and Maguire's uses vacuum technology.
UNIVERSAL DYNAMICS INC.
Universal Dynamics Inc., Woodbridge, Va., has introduced GenesysR, its new drying system for PET used in preforms.
Una-Dyn's parent, Piovan SpA, Santa Maria di Sala, Italy, first presented GenesysR to customers during the K show in October. It uses "reactor drying technology," which combines the benefits of rapid heating of the PET with an automated system that ensures the injection molding machine's injection pressure won't fluctuate due to moisture in the resin.
"The reactor drying technology is a brand-new development of Piovan that combines the benefits of using a reactor-type vessel in place of a traditional drying hopper, along with the advanced capabilities of a Genesys twin-bed, desiccant-type, dry-air generator," said Giorgio Santella, Piovan's chief marketing officer. "The two together are the GenesysR system."
The use of a reactor vessel reduces the drying time from seven hours to five hours and significantly increases the energy efficiency compared to a conventional drying system. A reactor vessel speeds drying by allowing for better air distribution and more rapid heat transfer.
GenesysR's operating temperature ranges from 340 to 355 degrees Fahrenheit. While similar to solid-state polymerization (SSP) technology, the GenesysR dryer operates at lower temperatures and the process does not increase the intrinsic viscosity of the PET.
The GenesysR system yields energy savings of about 60 percent compared to a conventional drying system, Santella said. It is particularly suited for high-volume applications, where the benefits of its low-energy, highly stable process can be maximized.
The line includes a patent-pending invention called Automatic Injection Pressure Control (AIPC), which allows any GenesysR system to be connected to a preform injection molding machine to read the injection pressure in real time. A new algorithm specifically developed for the AIPC allows GenesysR to constantly adjust airflow, temperature and dew point of the processing air so the injection pressure won't fluctuate, according to the company. The moisture level of the PET can affect the injection pressure.
GenesysR is an auto-adaptive drying system capable of determining the proper energy balance, or heating of the resin, according to the characteristics of the PET and the preform. Auto-adaptability allows the use of multiple grades of PET from different suppliers. The system self-adjusts to efficiently dry PET for preforms with very stable physical and mechanical characteristics that make the stretch blow molding process smooth and consistent.
The new GenesysR systems will be offered in addition to, and not in place of, existing Genesys drying systems
Ten GenesysR beta installations have been functioning for the last nine months, and the first GenesysR systems will be available commercially in the first quarter of 2017.
COMET PLASTIC EQUIPMENT
In October, Comet Plastic Equipment LLC, Riviera Beach, Fla., introduced its 3DX-M "split version" micro compressed-air resin dryer designed for use with small and micro injection molding machines.
The new split version separates the process air module and the dryer hopper, which allows for more installation options and takes the weight off the injection molding machine. With the standard 3DX-M version, the dryer hopper is mounted on top of the process air module.
Like other versions in the 3DX-M line, the new split version is suitable for all types of plastics and works without a desiccant dryer or the need for cooling water. Maintenance and cleaning time are minimal because the dryers have no moving parts.
Three hopper sizes are available — 2, 4 and 7 liters — with throughputs ranging from 0.1 pound to 8.8 pounds per hour. Hoppers feature a double wall of borosilicate glass for optimal thermal protection.
Features include:
• processing air with a dew point of minus 13 degrees Fahrenheit. If needed for certain applications, such as the production of PET preforms, the dew point can be lowered to minus 85 degrees Fahrenheit;
• an energy-saving, modular design for plug-and-play installation;
• a built-in, compressed-air filling/loading system;
• a programmable timer; and
• a large display that can be read up to 40 feet away.
MAGUIRES PRODUCTS INC.
Maguire Products Inc., Aston, Pa., introduced its VBD 300 dryer at the K show. It's an addition to the existing VBD line, processing up to 300 pounds of resin per hour. It falls between the previously available VBD 150 and VBD 1000 models, which process up to 150 pounds per hour and 1,000 pounds per hour, respectively. In the future, the company plans to introduce 500- and 700-pound-per-hour versions to fill out the line.
The VBD dryers use vacuum technology, which offers advantages compared to desiccant drying, said Frank Kavanagh, VP of sales.
"We're able to dry material in one-sixth the time of a conventional dryer, using one-third the energy," he said. "That is the advantage of vacuum drying."
The VBD line of dryers also reduces the number of moving parts compared to earlier versions of vacuum dryers, he said. Earlier models used rotating canisters that indexed through three different positions: a heat stage, a vacuum position, and a material take-off position.
However, the VBD line eliminates the movement of canisters and instead uses gravity to move the resin through the three positions. The vessels for each stage are stacked one above the other. As each phase is completed, a gate opens, allowing the resin to drop into the canister below.
"We're moving the material through the three different positions now, rather than moving the canisters through the three different positions," Kavanagh said.
Additional advantages include the use of load cells in both the vacuum vessel and the material-retention hopper, which allows for automatic regulation of the material through the drying system based on process demand. Load cells are used to weigh the amount of material in a chamber or hopper and then report the weight reduction that occurs over time as the process consumes the material.
The system also "blankets" the dried resin in the material retention hopper with air with a dew point of minus 40 degrees Fahrenheit to keep it from reabsorbing moisture.
In addition to the VBD 300 dryer, Maguire also introduced an optional touch screen controller for its entire line of VBD dryers in October as a replacement for the traditional analog version.
"People like the graphics and like the touch screen these days," Kavanagh said. "It's a nice graphical interface. It's more intuitive."
It also eliminates the need to decipher some codes that are displayed on the analog screen.
Bruce Geiselman, correspondent
Contact:
Comet Plastic Equipment LLC,561-842-0011, www.cometpe.com
Maguire Products Inc., 610-459-4300, www.maguire.com
Universal Dynamics Inc., 703-490-7000, http://unadyn.piovan.com
Bruce Geiselman
Senior Staff Reporter Bruce Geiselman covers extrusion, blow molding, additive manufacturing, automation and end markets including automotive and packaging. He also writes features, including In Other Words and Problem Solved, for Plastics Machinery & Manufacturing, Plastics Recycling and The Journal of Blow Molding. He has extensive experience in daily and magazine journalism.
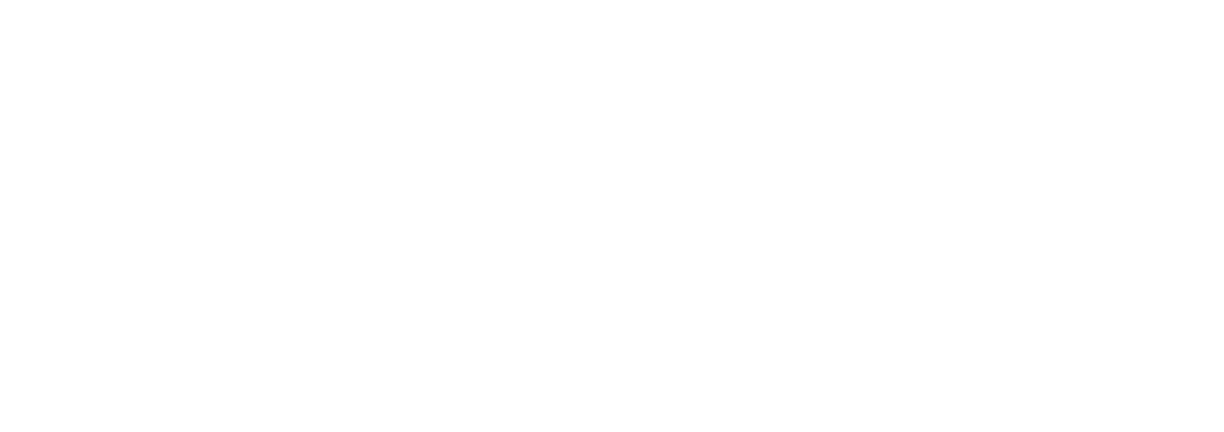