Injection molding machine suppliers based in China, South Korea, Brazil and Italy unveiled their latest innovations at last year's K show.
The companies' hydraulic machines are targeted at packaging, automotive and technical molding jobs, applications with long or short cycle times, and molding projects where energy savings is a priority. The firms continue to find value in equipping their presses with ball screws, linear guides and servomotor or pump designs familiar to North American and European injection molders. At least one company updated its machine controller.
ROMI LINE TACKLES PACKAGING, AUTOMOTIVE APPLICATIONS
Industrias Romi SA, Santa Bárbara d'Oeste, Brazil, launched the latest version of its EN line of servo-hydraulic injection molding machines. Updates facilitate more accurate machine movements while delivering more power and speed, compared to the previous version.
Romi's EN line is suited to molding technical parts, packaging or automotive items, and can be used for multimaterial injection. Special EN models are available for PVC and PET processing.
The base EN line includes 11 models with clamping forces ranging from 88 tons for the EN 70 model to 1,210 tons for the EN 1100 model. The EN line provides excellent repeatability of machine movements regardless of whether the product cycle time is short or long, said Neil Bathard, national sales manager for Romi. The accuracy and repeatability of the EN model can reduce part weight deviation, saving up to 2.5 percent in raw material costs, Bathard said.
The EN line uses servomotors to drive fixed-displacement pumps along the major axis of motion. Models with clamping forces of more than 600 tons are designed with double servo pumps that allow clamping and injection movements to overlap, thereby increasing machine productivity by 20 percent.
The double servo pumps also provide a higher ratio of injection and greater plasticizing capability, and can achieve faster closing movements. Linear guides on the injection and clamping unit minimize friction to enhance operating speed and precision.
Servo control of the short hydraulic circuit for all major motions in the injection unit, combined with a strong, rigid design, result in precise and repeatable machine movements accomplished with less power consumption than a fully hydraulic or variable-speed hydraulic system.
Romi's new CM20 control panel, designed for high processing speed, is standard on the new version of the EN line. The control has a full HD 19- inch multitouch graphical interface with updated software that improves the precision and speed of the machine through faster communication.
The controller can incorporate complex programming sequences more easily. Machine connectivity has been enhanced with software and hardware improvements that allow for access to the control through a browser, tablet or smartphone.
The unit can interface with manufacturing execution systems, remote services and other equipment and resources for Industry 4.0 connectivity.
Romi Machine Tools USA, Erlanger, Ky., represents Romi in the U.S.
WELLTEC TARGETS GENERAL-PURPOSE JOBS WITH NEW LINE
Welltec Machinery Ltd., Hong Kong, updated its Se II line of servo-hydraulic toggle presses for general-purpose molding with the new Se III series, sales manager Roy Chan said. The company showed a 260Se III model at the K show; it was producing a 206-gram, PP toy bucket made in a single cavity in a cycle time of 20 seconds. The bucket was labeled in the mold.
Due to hardware and software upgrades, the Se III model is more energy-efficient, stable and reliable. Features include more precise nozzle temperature control, which helps to reduce instability of the injection machine stemming from processing variables. A low transformation mold-clamping system allows for more precise molding. Chan said that the upgraded model is capable of faster screw revolutions and injection speeds and greater volumes. Greater tie-bar spacing accommodates larger molds.
Welltec, which is represented in North America by Welltec North America, Pacific, Mo., plans to roll out additional Se III models with clamping forces up to 1,100 tons by the middle of the year.
Welltec said the Se line typically uses a heavy-duty clamp that handles oversized platens and features a central automatic lubrication system. The injection unit has a quadruple tie-bar unicast construction supported on a precision-fabricated, high-tolerance sled that moves on a heavy linear rail system. The user-friendly controller incorporates a closed-loop double-feedback control and operates at fast processing speeds.
WOOJIN PLAIMM UPDATES CONTROLLER FOR CAPABILITY BOOST
Woojin Plaimm Co. Ltd., Jangan-myeon, South Korea, a manufacturer of injection molding machinery, launched a new machine controller. The pp580 is a web-based PC platform that allows remote connectivity and can monitor other equipment in the work cell, such as a robot, said Paul Hokkanen, technical sales manager. It has a membrane keyboard.
The controller can network with equipment operating with the Open Platform Communications-Unified Architecture protocol. The controller interface allows users to access data through touch, hold and slide gestures. Users can access pull-down menus, graphic icons and tutorials through its 15-inch display. The most common operating parameters are displayed on the main menu pages, but users can easily find other machine settings.
The controller will be available later this year on Woojin Plaimm's TH-A5 series of servomotor-driven hydraulic toggle presses, which have clamping forces from 55 to 500 tons, and for its upgraded DL-A5 series of two-platen, direct-locking horizontal presses, with approximately 500 to 3,300 tons of clamping force. It will also be offered on the company's VH insert molding machines, which range from 55 to 165 tons, and the TE-A5 all-electric models, with clamping forces of 30 to 850 tons. In the U.S., the company does business as Woojin Plaimm Inc., Mount Prospect, Ill.
PLASTIC METAL updates SERVO MODEL
Plastic Metal SpA, Vicenza, Italy, enhanced the mechanics of its Multipower hybrid injection machine line to make it more robust and efficient, managing director Marzia Virginio said. The company says the versatile, hybrid Multi-power line, available in clamping forces of 50 tons to more than 3,000 tons, performs well while using as little as half the energy of competing systems.
The Multipower line features brushless electric-motor-driven plasticization. A hydraulically balanced rotary piston powers the injection movement. A servo valve in the hydraulic circuit provides closed-loop control of injection speed, pressure and back pressure. An inverter controls the electric motor for the pump to recharge the accumulators (switching off/on) in order to minimize power consumption, while delivering high-speed, precise and repeatable operation.
The Multipower features a five-point double-toggle clamping unit. The Multipower HE version has electric clamp-opening and -closing movements; it uses a servomotor to control a ball screw driving the toggle. An electric drive system provides additional control and programmability. The company also offers Multipower in an H version where a hydraulic piston actuates the opening and closing of the clamp. In either approach, the clamp is designed to optimize force distribution during molding.
Plastic Metal is looking for a sales agency and assistance to develop its business activity in North America.
L.K. MACHINERY DEMONSTRATES LARGE PACKAGING WITH IML
L.K. Machinery Group, a Hong Kong-based supplier of injection molding, die-cast and CNC machines, demonstrated the flexible performance and energy savings of its new Forza III series of two-platen servo-hydraulic machines in the production of a large part labeled in the mold.
L.K. Machinery's Forza III series is designed for packaging and automotive molding applications, whereas the Forza II series targets houseware, appliances and electronics, said Leo Tung, a sales manager in the overseas sales department. The Forza III line, which has clamping forces of approximately 495 to 3,850 tons, features modifications to the screw size, servomotor and daylight between the platens. Its primary application is the manufacture of automotive spare parts, including instrument panels or fascia, as well as pallets, large garbage bins or plastic containers.
At the K show, L.K. Machinery demonstrated a unique application, producing a 20-liter pail, molded with both inside and outside labels in a cycle time of 18 seconds. The molding cell included an L.K. Machinery Forza III PT450H unit (with 495 tons of clamping force), with the in-mold labeling (IML) automation and robot supplied by partner companies. L.K. Machinery demonstrated that IML can be performed even while making a large part with short cycle times and low energy consumption using a smaller two-platen press. Such a part is typically molded on a press with a minimum of 850 tons of clamping force, Tung said. The turnkey IML cell for large-part molding required just 0.3 kilowatts. L.K. Machinery said servo-driven components reduce energy consumption.
A Keba controller managed the entire turnkey system. The unit featured a single injection cylinder based on a European design that improves speed and response time. It also has closed-loop control of pump output for energy savings and a noncontacting moving platen and tie-bar design that reduce premature wear.
The U.S. division of L.K. Machinery is LK Systems Inc., Ladera Ranch, Calif.
Mikell Knights, senior staff reporter
Contact:
LK Systems Inc.,949-375-0585, www.lksystems.us
Plastic Metal SpA, 39-0444-440-320, www.plasticmetal.it
Romi Machine Tools USA, 859-647-7566, www.romiusa.com
Welltec North America, 913-486-9211, www.welltecna.com
Woojin Plaimm Inc., 708-606-5536, www.woojinplaimm.com
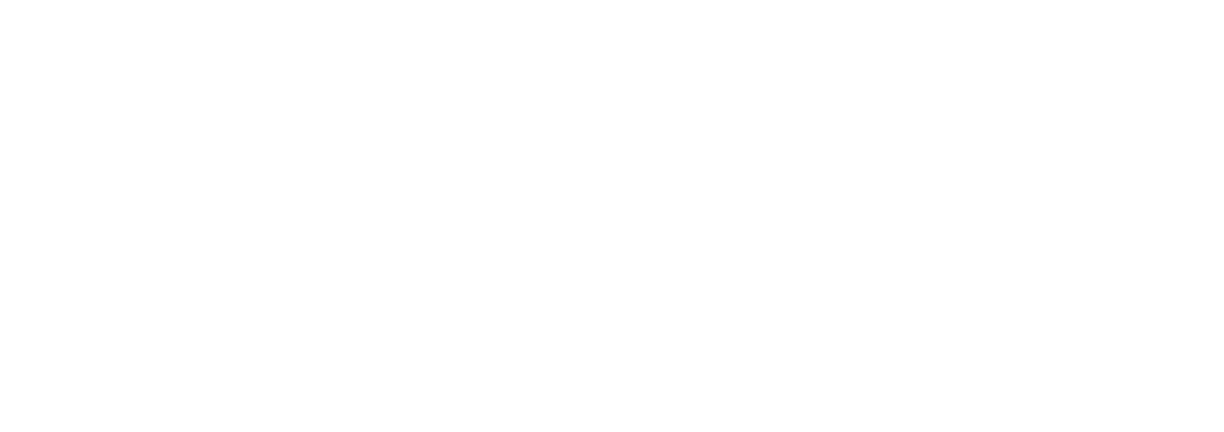