Blown film extrusion technology reached new heights during the K show. Key themes were better-performing films, technologies that allow for shorter production runs and improved cooling.
Several companies that couldn't display full lines offered tours at offsite facilities. Kuhne Anlagenbau GmbH bused show attendees to its facility in Sankt Augustin, Germany, to demonstrate its first 13-layer triple-bubble film system. Adolfo Edgar, Kuhne VP of blown film systems for the U.S. and Canada, said the technology is a multistage process that is used to produce biaxially oriented barrier films.
Until recently, he said, films made by the triple-bubble process tended to be relatively narrow and were used for sausage casings and barrier shrink bags. The films were not wide enough to compete with the barrier films made by conventional (air-cooled) blown film lines or even by the cast film process. However, over the past few years, Kuhne has been working toward widening those films.
Infrared (IR) reheating and annealing are used in the triple-bubble process. In the first step, a film bubble is made by extruding a tube downward. The bubble is water-quenched to create an amorphous structure with very low crystallinity, Edgar said. That structure is necessary to make it possible to simultaneously orient the film in two directions in the next step, and to allow for outstanding optical properties in the final product.
In the second step, the now-cooled film passes by IR heaters, and is blown into a wider bubble that is oriented simultaneously along two axes. The orientation has to happen simultaneously, not sequentially, to get the best film properties. Guarding against machine-direction orientation is key.
In the third step, the now-biaxially oriented film is reinflated at a lower pressure and then reheated with IR heaters. This is the annealing process, also known as thermofixation. This stabilizes the film structure and determines the amount of shrinkage possible in the final product, such as shrink bags or films used for lids, according to Kuhne.
Edgar said there are many opportunities for 13-layer, triple-bubble film, including ultra-high barrier applications in which an 11-layer structure is enhanced with layers of PP to protect the ethylene vinyl alcohol (EVOH) from humidity and prevent the deterioration of the EVOH's oxygen barrier properties. The film also could allow for the perfect pigmentation of a pouch while maintaining excellent barrier properties.
Hosokawa Alpine
Hosokawa Alpine Aktiengesellschaft, Augsburg, Germany, took the challenge to see how many layers could be produced at the trade fair. The company displayed an 11-layer system for the first time at a K show. Hosokawa's patented X-Die spiral-die design is behind the achievement, said David Nunes, president of Hosokawa Alpine American Inc., Natick, Mass. Hosokowa arranged 11 extruders to make the most of the system's footprint, and produced barrier films during the show. The individual layers of the barrier film and total thickness were measured by an NDC Technologies Inc. inline scanner.
Windmoeller & Hoelscher Corp.
For Windmoeller & Hoelscher Corp., Lincoln, R.I., "innovations are always borne out of production challenges," said Julian Banse, regional manager, technical sales, Africa, in an interview at the K show. At the show, officials showed the company's Turboclean technology on a five-layer Varex II blown film line. The Turboclean technology was fully automated, managing the resin changes on its own. Traditionally, that function has been performed manually by an operator.
"Only the required material is loaded into the system," Banse said.
All the processes of the machine are fully integrated and, via a touch-screen panel, the resin changes are completed in just a few minutes. Officials estimate that uptime is increased by 6 percent. This is due to a combination of a carefully designed algorithm and the automatic cleaning of gravimetric and vacuum conveyors. During the show, the company illustrated the change by switching from blue film to red.
ADDex Inc.
Several companies introduced air rings. Addex Inc., Newark, N.Y., showcased its new air ring, which uses one of four cooling elements from the company's Intensive Cooling Experience (ICE) technology. The new dual-flow design is focused on increasing output without sacrificing quality, Addex President Bob Cree said during an interview at the K show. The company guarantees an increase in output rate of 10 percent to 15 percent; what users actually experience is typically 15 percent to 20 percent. The dual-flow design has two primary locking points instead of one, and that improves bubble stability.
The dual-flow air ring with ICE is geared toward the retrofit market; the ICE technology also applies to all of Addex's air-ring products, including its automatic profile external gauge control (EGC), manual gauge control and laminar-flow air rings. The company also has developed a triple-lip design that provides three primary locking points. The automatic profile EGC now also is being used by OEMs, and Cree is seeing a shift from use on the retrofit side to OEMs.
Addex used to sell complete blown film lines, but it now is focused on cooling. Its largest market is North America.
"It has helped us tremendously," Cree said. "The customers drove that. It definitely was the right thing for us to do."
Brampton Engineering Inc.
Brampton Engineering Inc., Brampton, Ontario, spotlighted its Vector Air Ring. CEO Gary Hughes said that it has a single air inlet, compared to other air rings that have multiple inlets.
"Immediately, putting this new technology on anyone's die, the film thickness reduces, before we even start gauge control," Hughes said during a tour of the company's booth at the K show.
The new design offers better blown film cooling with lower pressure losses, and repeatable, recipe-driven setups. Brampton used computational fluid dynamics to streamline the flow of chilled air for what the company calls exceptional uniform cooling around the bubble.
The air ring shows operators the flow rate and the pressures at all times. "We've made that all digital. So once that is set up for that recipe, it's digitally stored, so the next time, next month, next week, that you come back to that film order, it's set. You don't have a different operator trying to figure this out, which wastes material and wastes time and risks quality," Hughes said.
Brampton also unveiled its SCD 4.0 die technology. The coextrusion technology allows a processor to produce each polymer at its ideal temperature. Four different options allow temperature differences between adjacent layers ranging from 27 degrees to 162 degrees Fahrenheit, which minimizes degradation.
"The days when a die runs a certain set of resins and it always runs the same structure, they're going away," Hughes said. "Our clients will come to us and say, 'Well, I want a die and it has to run these 10, 20 different structures.' The nylon may move from the center to the outside and then we may have EVOH there, then nylon. The structures are getting more complex. That is how our customers differentiate. They will make films very specific to a customer."
Through this technology, Brampton is managing temperature and residence time. As an example, the barrier layer might be EVOH. That likes to run at 428 degrees Fahrenheit. But next to it, a processor may want a nylon layer. The nylon likes to run at 482 degrees Fahrenheit.
"Conventional barrier dies, they will run the whole die at the nylon temperature," he said. "They have one temperature. Or they may run heater bands at different temperatures but the steel is all touching. We separate it. So the EVOH can run at its ideal temperature. It's very sensitive to temperature. So we're managing the temperature. So what that means to our client is that they can run longer between die cleans. They have less degradation-related quality issues."
Angie DeRosa, managing editor
Contact:
Addex Inc., 315-331-7700, www.addexinc.com
Brampton Engineering Inc., 905-793-3000, www.be-ca.com
Hosokawa Alpine American Inc., 508-655-1123, www.halpine.com
Kuhne USA, 416-700-7444, www.kuhne-ab.de
Windmoeller & Hoelscher Corp., 401-333-2770, www.whcorp/us
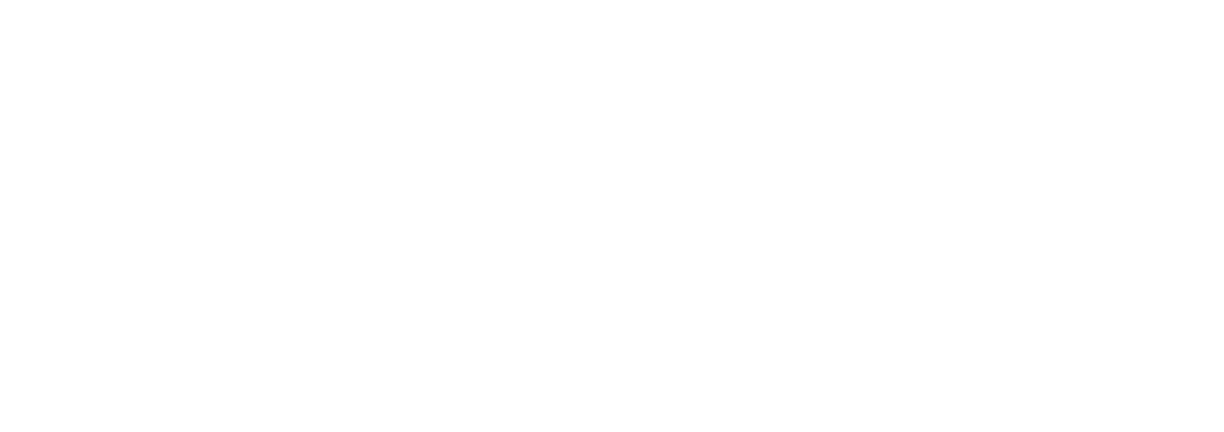