At the K show, Next Generation Recyclingmaschinen GmbH, Feldkirchen, Austria, and Kuhne GmbH, Sankt Augustin, Germany, introduced the P:Sheet system, which shreds PET waste, converts it into polymer melt and then extrudes it into sheet.
The shredder-feeder-extruder combination can convert any form of PET scrap into high-quality melt, according to NGR. In fact, three lines that have already been sold use PET fiber scrap as the feedstock. Another uses sheet scrap from extrusion lines. Bottle flakes also can be used.
The PET melt is decontaminated in NGR's P:React liquid-state polycondensation unit so that it meets FDA regulations for food-contact applications. The intrinsic viscosity (IV) can be specified. "This means all the material requirements are on hand for producing PET sheets that have tight IV tolerances on par with virgin material," NGR CEO Josef Hochreiter said.
The final component is a sheet extruder from Kuhne.
"Initial tests have far exceeded our expectations for sheet quality," said Hubert Armbruster, managing director of Kuhne. "The newly provided option for producing high-quality PET sheets from low-cost input materials, and eliminating one melt step in the process, have already ignited great interest among our customers," Armbruster said.
"The PET sheets show significantly better performance in thermoforming as the IV values may be tailored to the specific application and are in a very narrow band," said Michael Heinzlreiter, CMO at NGR.
At its K show exhibit, NGR also introduced the T:Cracker, which takes solid residues from washing lines in plastics recycling operations and converts them into fuel.
"This technology addresses the high costs that recyclers have to pay for sludge going to landfills," Heinzlreiter said.
Called a "material morphing technology," the T:Cracker reaches temperatures of 842 degrees Fahrenheit to split chains of hydrocarbons into a gas/oil mixture to produce energy as well as solid products such as coke or calcium carbonate.
NGR developed the process in partnership with Johannes Kepler University of Linz, Austria, which is operating customer trials at a test unit on campus. NGR is marketing the T:Cracker technology through its new business, NGE Material Morphing Technology.
In other recycling-related K show news:
Starlinger & Co. GmbH, Vienna, introduced technology that reduces unwanted odors in recycled resin pellets. Targets for removal include residual chemicals from food, cosmetics or detergents as well as residues from monomers, oxidation, hydrolysis and volatile organic compounds.
Recyclate is heated and homogenized in the first step of the process. In the second, gases are removed in the Starlinger C-Vac degassing module, which increases the melt surface by 300 percent, the company said. Treatment in the Smell Extraction Unit is the final step.
At the company's stand, visitors could take whiffs of both treated and untreated materials, include regrind from HDPE gas tanks.
"This process will create commercial markets for materials, such as fuel tank recyclate, which did not exist before because of the odor issue," said Alan DiUmberto, sales manager, recycling division, American Starlinger-Sahm Inc., Fountain Inn, S.C.
Erema, Ansfelden, Austria, also introduced odor-reduction technology for polyolefins at the K show. Refresher, an airflow system that blows odor off pellets, is now an option for the firm's Intarema TVEplus extruder.
"Odor treatment is of the highest relevance for post-consumer recycling in order to increase the number of application fields for the respective recyclates," said Clemens Kitzberger, business development manager for post-consumer recycling at Erema. The technology is especially applicable in the automotive and electronics markets, but fits elsewhere as well.
Pallmann Maschinenfabrik GmbH & Co. KG, Zweibrücken, Germany, introduced Recycling Extruder ECO 70, which accepts HDPE and LDPE film as edge trimmings or tangled film, or in baled form.
A pre-shredding system cuts the material into flakes, which are fed into an extruder screw through the rotor of the shredder. The recyclate is melted and homogenized by the screw before moving through a filter designed to retain any solid impurities such as paper. Pellets are approximately 0.16 inch in diameter. The melt then goes into a hot-die pelletizer. A degassing unit is available as an option.
Gamma Meccanica SpA, Bibbiano, Italy, showed an upgraded GM65 Compac line at the K show. The Compac system is designed to process difficult-to-recycle materials such as film, fiber, fabric and yarn. The system comprises a feeder equipped with a cutter-compactor, an extruder, screen changer and pelletizer. The newly upgraded Ecotronic control allows the machine to handle material with high residual moisture (up to 10 percent) and heavy print, said Maurizio Burini, export sales manager. The extruder has a degassing station with two ports. New screw designs increase throughput, Burini said.
Dosing and color hoppers can be used to add properties to the material during processing.
Recycling coverage from the K show will continue in the March issue of Plastics Machinery Magazine with an examination of Recycling 4.0 and other approaches to the smart recycling factory.
Doug Smock, senior correspondent
Contact:
American Starlinger-Sahm Inc., 864-297-1900, www.starlingersahm.com
Erema North America Inc., 978-356-3771, www.erema.net
Gamma Meccanica North America, 864-675-0775, www.irecyclingsolutions.com
Next Generation Recycling Machines Inc., 678-720-9861, www.ngr.at
NGE Material Morphing Technology, 43-7233-70-107-0, www.nge.at
Pallmann Industries Inc., 973-471-1450, www.pallmann.eu
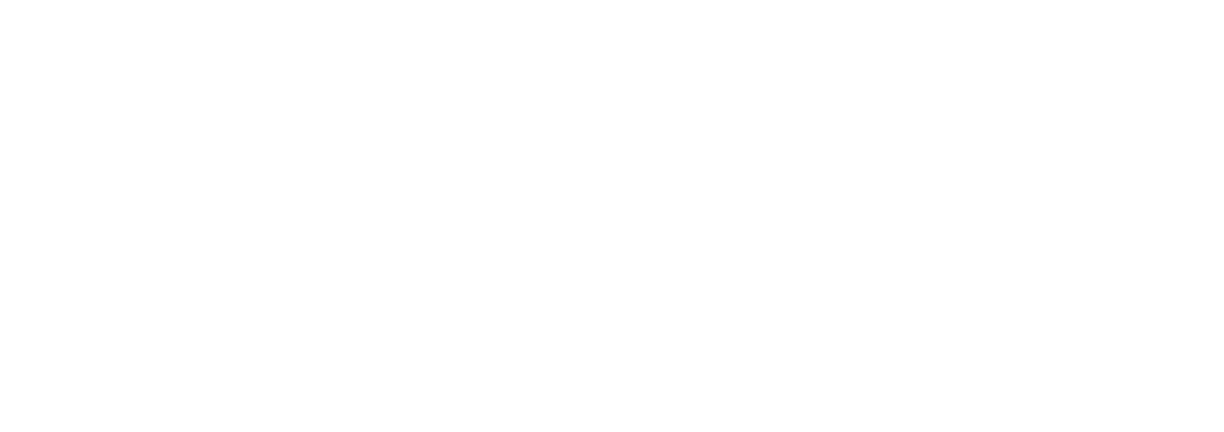