Jomar Corp. is launching a new series of injection blow molding (IBM) machines designed to incorporate the energy savings associated with all-electric models without the additional expenses for parts.
"We've achieved the precision and energy savings of an all-electric machine, but we've been able to preserve our hydraulic system, which is extremely robust and doesn't have the huge replacement costs associated with direct-drive electric components," Jomar sales manager Ron Gabriele said. "In our estimation, we've captured the best attributes of all-electric and hydraulic machines and combined them in the IntelliDrive series."
Combining electric servomotors and hydraulic power allowed Jomar, Egg Harbor Township, N.J., to provide the benefits of electric motors, which typically take up more space, without enlarging the machine's footprint. The initial cost for IntelliDrive machines will average 10 percent to 15 percent more than standard hydraulic models, but the costs of replacement parts for the IntelliDrive units will be comparable to those for traditional hydraulic machines.
"We feel the IntelliDrive Series makes more sense for our customers who want energy savings, but not expensive and complicated repairs," said Jomar President Carlos Castro.
The series features precise, servo-driven hydraulics that reduce energy consumption by 40 percent to 50 percent and has a dry cycle time of 1.8 seconds, about one-half second faster than standard hydraulic machines.
"The whole point of the machine series is it makes bottles cheaper through reduced utility costs," Gabriele said. "On top of that, since we have been able to make the machines run faster, we can actually make more bottles. So, we are making more and cheaper bottles. It is a home run."
Jomar's IBM machines primarily make bottles for the pharmaceutical, health care, personal care, beauty, food and beverage and household products industries.
Servo-driven hydraulics combine electric servomotors and hydraulic power. In a standard hydraulic machine, one electric motor drives both the plastifier and the clamp pressure, whereas the IntelliDrive divides those two functions between two smaller motors. At NPE2015, Jomar teamed up with engineers from Bosch Rexroth, Lohr am Main, Germany, to discuss how Jomar could incorporate Rexroth's servo-driven hydraulic technology into IBM machines. The companies established a goal of introducing a line of energy-efficient machines at K 2016. The new machines incorporate a Rexroth servomotor in conjunction with a Rexroth hydraulic pump.
The IntelliDrive plastifier is directly driven by a hydraulic radial piston motor, which in turn gets power from a servo-driven hydraulic pump. This develops only as much power as required to perform a particular job. While the hydraulic pump on a standard machine is always running, a servo-driven pump can increase or reduce the power as needed. That is the source of the majority of the power savings.
A separate electric motor on the IntelliDrive machine drives the remainder of the machine functions, including the clamp. This motor is controlled by a variable-frequency drive, which also reduces power consumption and noise.
"In general, the IntelliDrive machine is a lot smarter in its use and consumption of power," Gabriele said. "That's the origin of the machine's name."
In addition to power savings, the machines require 40 percent less hydraulic oil, use about one-half the cooling tower water and emit substantially less heat, resulting in operating costs that are dramatically lower than standard hydraulic machines.
The IntelliDrive machines feature a reinforced platen as well as a new clamping system that provides more precise control over the clamp's speed and position. The goal is to prolong the lifespan of the molds and prevent platen deflection or warping.
Jomar is unveiling its new technology at the K show this month in Düsseldorf, Germany. The company will display a single prototype machine, the Model 85S, which is capable of applying 72 tons of pressure to molds. The company has a potential buyer for the prototype, which likely "will not be coming back from the show," Gabriele said.
Jomar also is ready to take orders on a larger IntelliDrive Model 135, which has a clamping force of 135 tons. Later this year, Jomar plans to introduce the technology to a Model 65 and a Model 175 that will apply 65 and 175 tons of pressure, respectively.
Another new development is a quick-change mounting system for the preform cylinder, which drastically reduces the time required for cylinder maintenance. With the new mounting system, the cylinders can be removed individually, making it easier to access and service any of the three cylinders.
Jomar officials are so confident in the hydraulic system of the IntelliDrive series of machines that they have extended the warranty to 30 months from the standard 12 months, Gabriele said.
Bruce Geiselman, correspondent
Contact:
Jomar Corp., 609-646-8000, www.jomarcorp.com
Bruce Geiselman
Senior Staff Reporter Bruce Geiselman covers extrusion, blow molding, additive manufacturing, automation and end markets including automotive and packaging. He also writes features, including In Other Words and Problem Solved, for Plastics Machinery & Manufacturing, Plastics Recycling and The Journal of Blow Molding. He has extensive experience in daily and magazine journalism.
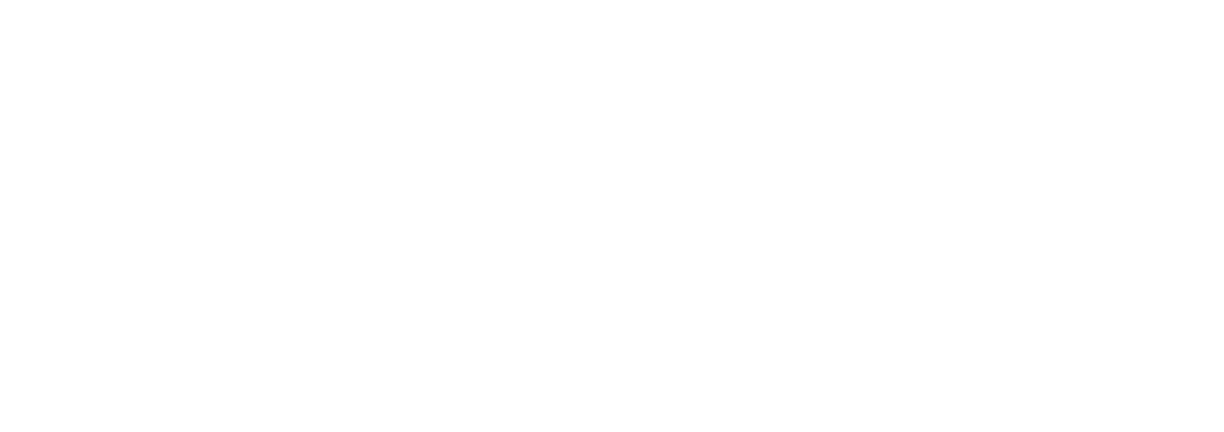