A new system is aimed at boosting quality control of the insert molding process.
Fanuc Corp., Oshino, Japan, filed a patent application for a system that allows inspection of an insert part prior to injection of resin into the mold. The invention involves the output and recording of inspection data in conjunction with traditionally recorded data on the injection molding cycle, such as pressure, temperature and screw position.
In two iterations of the technology, devices attached to an insertion robot visually inspect the insert part or measure its weight. The purpose of the visual inspection is to look for discoloration, silver streaks, voids, weld lines, flow marks, bubbles, jetting or contamination.
The patent application states that "the method for directly inspecting molded articles (by workers) generally requires much labor and cost for the inspection." As a result, many molders use an indirect system tied to molding conditions. The Fanuc invention combines both direct and indirect inspection in an automated system.
Fanuc introduced its first injection molding machine in 1984. Milacron LLC, Batavia, Ohio, which helped develop Fanuc's electric machines in the 1980s, still has exclusive distribution rights for Fanuc Roboshot machines in the Americas.
Patent Application 20160193761; published July 7
In other patent news:
Thermoforming. Zubex Industrial SA de CV, Monterrey, Mexico, is developing a coextrusion system to produce trays with moisture- and oxygen-barrier properties. According to the patent application, coextrusion of three bubbles ensures the distribution of uniform thickness in the walls, base, folds and corners of the formed tray. This reduces the amount of plastic used by 50 percent without diminishing gas-barrier and puncture-resistance properties. Founded in 1984, Zubex is a manufacturer of plastic packaging.
Patent Application 20160200030; published July 14
Coextrusion die. Exxon Mobil Chemical Co., Baytown, Texas, has developed a technology to improve the quality of thermoplastic vulcanizates (TPVs) with different rheologies. The goal of the invention is to control the flow of extrudate in the die through use of a flow pool and a through orifice. The result is a smooth part that holds its shape; has no edge tear; has slight or no warpage; and does not have silver line, which is streaking on the surface often caused by excessive moisture. ExxonMobil's Santoprene TPVs are used as automotive weather seals and in other applications.
Patent 9,387,620; issued July 12
Integrated thermocouples. In this innovation, thermocouples are built into a hot-runner nozzle body to ensure accurate temperatures. The patent states: "Unitary monolithic integration of thermocouples allows thermocouple junctions to be located highly proximate to the locations where temperature monitoring is desired, particularly, near the tips of injection-molding nozzles, which has conventionally been difficult or impossible to achieve." The technology was developed by Husky Injection Molding Systems, Bolton, Ontario.
Patent Application 20160193770; published July 7
Tube winder. New technology has been developed to allow winding of empty plastic microduct tubes (2mm to 20mm) without crossover, which can create kinks in the tubes. According to the patent application, manual winding, which is frequently used, is neither efficient nor CE-compliant. The equipment described in the invention includes a tube-guiding device. The technology was developed by KraussMaffei Technologies GmbH, Munich, and Graewe GmbH, Neuenburg am Rhein, Germany.
KraussMaffei Berstorff produces extrusion machines and systems for manufacturing plastic pipe with diameters of 5mm to 2.5 meters.Graewe specializes in downstream extrusion equipment.
Patent Application 20160185027; published June 30
Doug Smock, senior correspondent
Patents and patent applications can be viewed at www.uspto.govHave you applied for or received a patent? Contact [email protected]
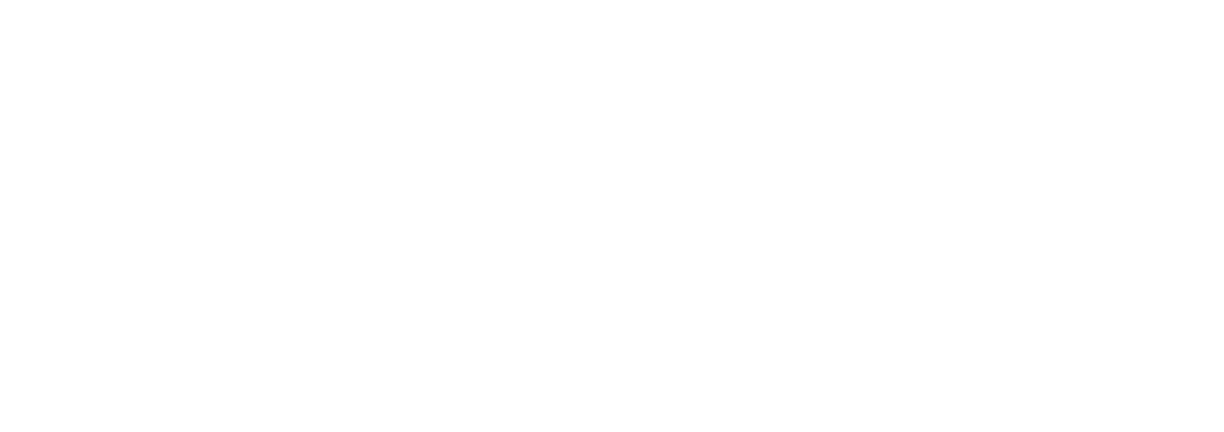