Inside the facilities of Good Works Reprocessing LLC (GWR) in eastern Pennsylvania, an array of carefully selected equipment does the gritty work of reducing post-industrial plastics that come in any form imaginable. There are garden hoses, there are rigid containers, there is TPO roofing and, on the day of Plastics Machinery Magazine's visit, there was a box containing flexible mannequin parts. Those heads, legs, arms, feet and hands will be processed through a Cumberland 50 Hog granulator with a Sterling Blower elutriation system, which will grind the flexible PVC. The regrind will go back to the manufacturer for use as filling in crash test dummies, explained GWR President Dan Sheehan.
It isn't the most challenging reduction he's seen since starting the company with his partners in 2010. The newest challenge has come in the form of HDPE boards that have to be shredded and processed to go back to the manufacturer, who will use the regrind in other boards.
GWR, Easton, Pa., is a custom size-reduction company whose services include pulverizing, blending, grinding, metal and contamination removal, repackaging, classifying, fines removal and certified destruction. To shred those boards, Sheehan brought in a shredder from Avian USA Machinery LLC, West Chicago, Ill. The ASG1500 Series single-shaft shredder was customized for GWR's needs. Avian designs this shredder model with a hopper opening of 64 inches by 59 inches and a volume of 81 to 162 cubic feet.
"All the other shredders I found were not able to do the board," Sheehan said. "The boards always were the biggest challenge."
Sheehan, who has been in the industry for more than 30 years, was most concerned about safety, especially for the company's 46 employees.
"Safety is one of the main things. I never want them to use a hand saw or table saw. I know what it can do. I trust myself with it, and I wouldn't do it," he said.
Focus on the rotor design
Avian's parent company, Avian Granulator Group, is based in Sydney, where it began in 1982. It has three manufacturing facilities worldwide: Shanghai, West Chicago and Sydney, where it engineers and builds machines. For GWR's needs, officials knew that a customized rotor design was going to be key and that an adjustable bed knife was paramount.
On the rotor design, there normally is one 40mm knife, said Andrew Dunn, senior sales engineer with Avian. In the design for GWR, Avian used two 30mm knives.
Dunn said that in some cases, if a machine doesn't have an adjustable bed knife, as the rotating knives wear out, you get larger and larger pieces of board. If the recycler has a small board, measuring 0.5 inch or 0.25 inch thick, it's going to pull it down between the rotor and the bed knife and jam the machine. Sheehan and his business partners strive to avoid machine jams.
"What happens is the board comes down, the rotating knives hit it, stand it straight up, and then it drags it down and jams between the rotor and the bed knife," Dunn said. With an adjustable bed knife, because the rotor knives wear a little, that gap is closed. That results in "higher production without the worries of jamming it up," he said.
The machine is the first installation in the North American market with that rotor design.
"We designed the machine based on what he needs," Dunn said. "This was guaranteed for the boards. We quoted the shredder based on the boards. But then the big question is, will it work with everything else? The answer is yes."
The machine does not have a preprogrammed panel. Operating the machine without a preprogrammed panel is what Sheehan prefers because he and his team are not limited to what the machine is programmed to do. They can build in variability based on the given materials.
"It's got the beef behind it, it really does," Sheehan said. "If you need a little more drive on some materials, you can put it in there. You can play with it, you can experiment with it. The boards were always a challenge. I like to push things to their limits. And then back off from there."
Quality comes first
GWR is owned by Sheehan and his four partners — VP Jose Martinez; brothers Rene Blanco and Enrique Blanco, who work in production; and Pedro Gonzalez, who handles maintenance. Their two buildings in Easton have 11 Cumberland grinders. Orenda Pulverizers Inc. supplied an H1D 500 pulverizer that takes regrind and grinds it down to a powder. GWR most commonly pulverizes to the size of a grain of salt or a 20 mesh, as it's known in the industry. The machine, however, is capable of grinding to a smaller size, said Sheehan.
Sterling's blower elutriation stations remove paper, fines and light contaminates from regrind. Sterling designed the system for simplicity of operation, according to the company, with "set-and-lock" inlet-gate features to control material flow and separation. The system can be fed directly from a granulator, bin or other source, eliminating the need for air-lock valves, screeners or other costly, high-maintenance mechanical equipment. The components of the system are modular and therefore can be designed in a custom layout.
For GWR, the most critical aspect in machinery selection is the quality of the machine and that the machine does what it's supposed to do. Though that sounds straightforward, Sheehan has experienced otherwise.
Dunn called the Avian shredder a simple system that gets the job done. The motor is belt-driven with a fluid coupling connection and it also has a soft-start motor starter in the control panel.
"It's a simple system, and sometimes simple is best," said Sheehan. "It's got enough bells and whistles to make it worth it."
Fiber removal specialty
Sheehan and company are very guarded about their specialty of fiber removal. Coils upon coils of garden hose sit ready for size reduction. The trick in the processing of garden hose is the fiber removal. The partners here became specialists in this during their time together at Nicos Polymers & Grinding Inc., which was based in nearby Nazareth, Pa.
"We did it well before; we do it better now," Sheehan said. "What makes Good Works a leader in fiber removal is experience, persistence and understanding that it is not always about pounds per hour."
Sheehan said that the company does a lot of fiber removal and it is an area where they have done a lot of tweaking for the equipment. The materials are sometimes processed through GWR's system two or three times in order to remove as much fiber as possible. The standard pieces of machinery used are granulators and an aspiration or elutriation system. But the final process, which is proprietary, is where the biggest difference occurs, Sheehan said.
"You have to put effort into it. There is a lot of tweaking and other secrets," he said.
Angie DeRosa, managing editor
Contact:
Good Works Reprocessing LLC, 610-923-3607, www.goodworksreprocessing.com
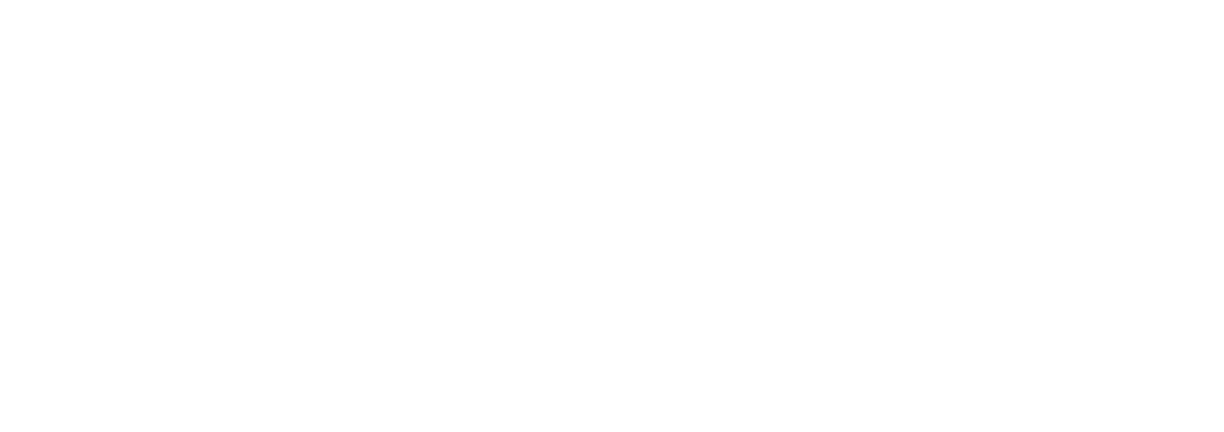