Since NPE, clear plastic cans have been getting a lot of attention in the plastics industry. Plastics machinery equipment maker Milacron Holdings Corp., Cincinnati, introduced its Klear Can, which is injection molded, at NPE. The plastics industry has been working to provide an alternative to metal cans because of changing consumer tastes and the demand by consumers to be able to see the products in their containers.
Now, another company is bringing its clear plastic can to the market but the production is done via extrusion. Sonoco Products Co. has introduced its TruVue clear can using the company's Fusion Freshlock technology. This homegrown extrusion technology is in operation at a pilot plant at Sonoco's headquarters in Hartsville, S.C.
The cans are produced from five-layer PP and EVOH tubing extruded on Sonoco's line, which Plastics Machinery Magazine covered in "On the Factory Floor" in June 2015. This is a convertible, coextrusion line that can produce tubing or sheet with up to seven layers. It is the same technology that is used to make Sonoco's adhesive and sealant caulk tubes. The line was first installed as a turnkey system at Sonoco's pilot plant about 13 years ago. Jeff Schuetz, staff VP, consumer packaging global technology, and his team recently added tubing capability to the line so that it can be switched back and forth to support either the sheet platform or the tubing platform. The newer tube die and the back-end components were made by different OEMs and integrated into the existing system by Sonoco. Sonoco is able to leverage the same front end and change the die and the cooling/haul-off system of the plastic to swing between tube and sheet.
Steve Gendreau, global plastics VP, sales and marketing, says the continuous extrusion process provides high outputs, consistent container and barrier layer thickness and low processing waste. To protect suppliers, officials say they can't disclose the OEMs.
The use of two metal ends on the can serves several purposes, Gendreau says. First, the can is designed to run on existing metal can processing equipment with minimal modification. This includes conveying, seaming, using magnetic elevators and rolling through continuous retort chambers. Secondly, the metal ends help the container hold its shape and improve heat transfer during the retort process, which involves high heat and high pressure.
Those metal ends allow for good rolling action through the continuous cooker, according to the company. This provides a uniform heating performance throughout the retort process.
Initial production will occur on the pilot line, which is being upgraded to increase automation and capacity, he says. The production line design is being finalized and these lines will be put into Sonoco's plants as the business grows.
The can has been field tested for three years across several applications. Processed and shelf-stable foods are the particular target, including soups, sauces, fruits and vegetables and in some cases, wet pet food. These are products that have been traditionally sold in metal cans on shelves in the center of a store. This area has been losing share to fresh products often found on the perimeter of the store. The container has passed shelf-life testing up to two years, he says.
Sonoco expects to see the first commercial launch, with product on shelves, in the late second quarter.
Angie DeRosa, managing editor
Contact:
Sonoco Products Co., 843-383-7000, www.sonoco.com
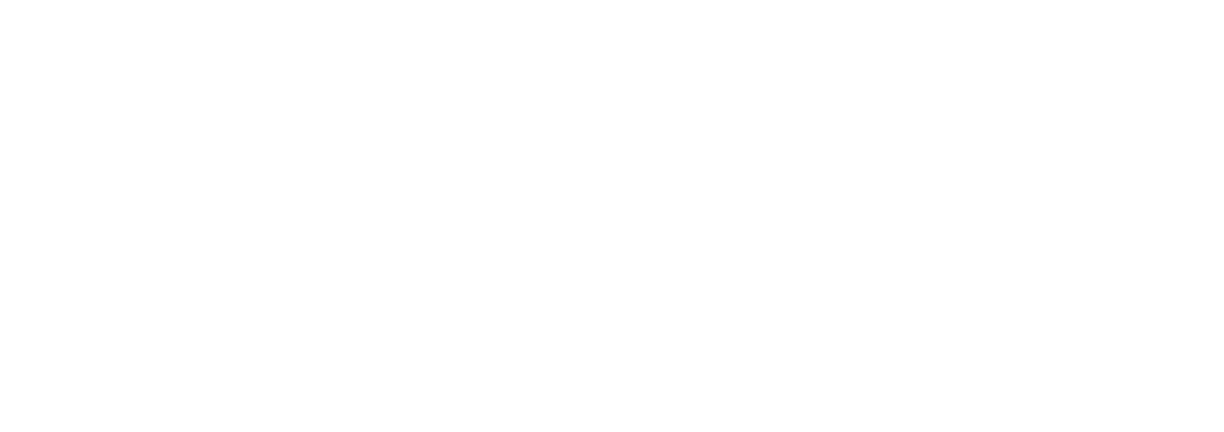