As a component of its FiberForm process, the KraussMaffei Group has introduced a precise metering system for highly concentrated long fibers.
The process, shown for the first time at Fakuma using a CX 300 injection molding machine, produced an airbag housing that was 47 percent lighter than the same part currently in production using short-fiber-reinforced material. "I think this is a huge performance," says Hans Golz, president of KraussMaffei's injection molding machinery business. In the process, endless-fiber fabric impregnated with a PP matrix was heated, then shaped in the injection mold and overmolded.
Munich-based KraussMaffei Technologies GmbH first announced the FiberForm process early last year. It combines injection molding with thermoforming of composite sheets to improve the strength of fiber-reinforced parts. Processing of long-fiber material integrated into the FiberForm process was new at Fakuma.
Flow problems are associated with precisely metering PP and an equal amount of PP long-fiber pellets made up of 60 percent fiber content. To solve them, KraussMaffei used two gravimetric dosing units. A C-Flex M feeder from Motan-Colortronic GmbH, Friedrichsdorf, Germany, previously used for extrusion, made uniform mass flow possible for the first time, KraussMaffei says.
"Fluctuations when setting the fiber content can be significantly reduced compared to conventional mixing concepts," says Jochen Mitzler, head of strategic product management at KraussMaffei.
The company says the ability to successfully process highly concentrated long fibers offers an economical lightweighting solution. Material cost is lower than using standard pellets. The finished part has high strength, so wall thickness can be reduced.
This precise metering means processors can adjust the procedure with greater precision, according to KraussMaffei. This is particularly important in manufacturing safety components — such as airbag covers — where uniformity and a reproducible process are needed.
Motan's C-Flex M is a flexible-walled feeder suited for dosing powders, pellets, granulates, regrind, fibers and flakes in both continuous and batching processes. Motan says the removable hopper can be quickly exchanged to facilitate cleaning and changing materials. Consistent screw fill is maintained and bridging eliminated by use of the flexible PU hopper that is activated by friction- free massage rolls.
The injection molding machine used for the demonstration at Fakuma was a CX 300 – 1400. Cycle time was less than 40 seconds.
The molding machine was equipped with two KraussMaffei LRX linear robots with Twin-Z design. The two robots were connected to the same Z-axis. The robots heat the semifinished composite sheets and demold the finished part.
The CX series injection molding machines' clamping forces range from about 35-160 tons.
NEW PU MIXING, METERING SYSTEM
KraussMaffei also showed a PU mixing and metering system for midrange applications at Fakuma.
The modular RimStar Compact 16/16 is designed to be used in different configurations. It can be integrated with or connected to multipoint metering, peripheral devices, material supply or robots. It is installed with the power-control cabinet on a one-piece machine frame and designed as a plug-and-play unit.
"The RimStar series is a master of versatility and is suitable for all areas of application of [PU] processing," said Steffen Bauer, sales manager of reaction process machinery.
The RimStar series has a discharge capacity of 40 to 550 grams per second with a mixture ratio of 1-to-1. The pump can put out 16 liters per minute. The product also has a small footprint. The Compact series has available discharge rates for polyol component and isocyanate component varying from 4 liters a minute for each component to 155 liters per minute for each component.
KraussMaffei says the high-pressure pumps used in the RimStar series were developed and produced in-house. They are wear-optimized and permit reliable metering of different matrix compounds.
The Compact 16/16 at the show was equipped with a Siemens control system with a TP 1200 control panel. Control through a mobile device is available as an option.
Ron Shinn, editor
Contact:
Krauss Maffei Corp., 859-283-0200, www.kraussmaffeigroup.com
Motan Inc., 269-685-1050, www.motan-colortronic.com/us
Ron Shinn | Editor
Editor Ron Shinn is a co-founder of Plastics Machinery & Manufacturing and has been covering the plastics industry for more than 35 years. He leads the editorial team, directs coverage and sets the editorial calendar. He also writes features, including the Talking Points column and On the Factory Floor, and covers recycling and sustainability for PMM and Plastics Recycling.
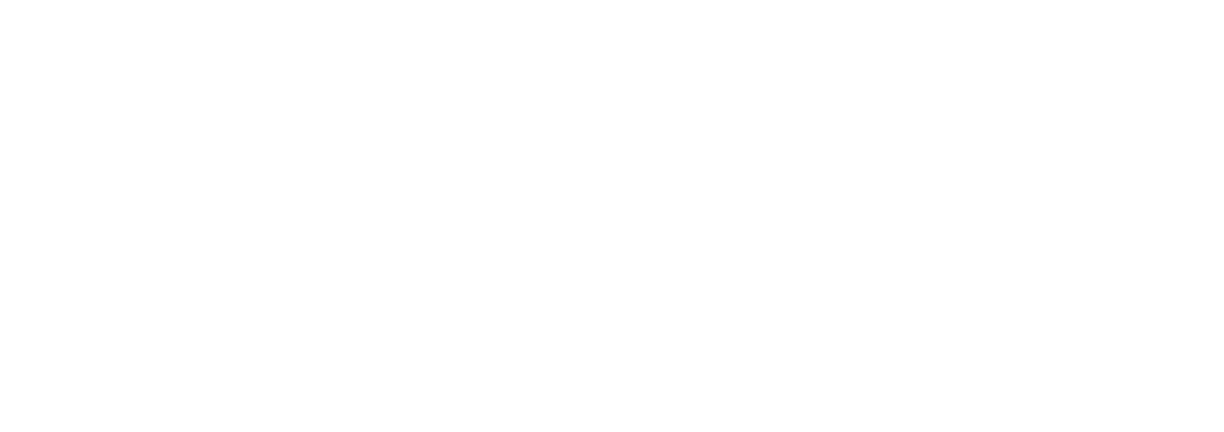