Dr. Boy GmbH & Co. KG, Neustadt-Fernthal, Germany, has unveiled its smallest plasticizing injection screw, only 8mm in diameter. It is aimed at micromolding applications where parts may weigh as little as .077 gram. The company showed the screw for the first time at Fakuma, and Thomas Breiden, marketing director, says it plans to begin producing them in 2016.
"This plasticizing screw is small, but it is not a lab model," Breiden says. "It is a standard screw designed to run 24/7."
The screw has a screw channel volume of 1.9 cubic centimeters. This results in a shorter residence time for the material, which is an advantage when processing thermally sensitive plastic. No pre-plasticization was required for the parts running at the show. Boy has applied for a patent on the screw.
At Fakuma, the screw was used to produce micro-osteosynthesis plates that weighed .078 gram. Residence time of the material in the plasticizing unit was 5 minutes and 4 seconds. These are surgically implantable plates used to repair bone fractures. They traditionally have been made of metal.
The new screw was running in a Boy XS machine with a clamping force of 10 tons. Cycle time for the polybutylene terephthalate material was 9.6 seconds.
Another Boy XS press was molding parts using a 3-D printed mold insert that was made in the booth. Boy used a Stratasys 3-D printer to make the inserts, which took about two hours. The insert then went directly from the printer to the mold base, where it was used to mold a glass-filled part — a carabiner. Cycle time was 90 seconds. Each 3-D printed mold insert can run up to 500 parts, depending on the material.
"This process is mostly being used now for prototyping," Breiden says. "But we are showing that you can easily produce parts with printed molds." He adds that glass-fiber-reinforced parts and fire-resistant parts can also be made.
"This also shows we can produce parts that you cannot make with just a 3-D printer," he says. "The parts we are making here have all the properties of a standard part, not a 3-D printed part."
The machine, 3-D printer and mold shown at the show cost less than $107,000, he said.
Another interesting operation Boy demonstrated at Fakuma was a two-component insert molding technique on one machine in automatic operation. One mold combined a hot nylon and cold liquid silicone rubber (LSR) to produce a screwdriver.
The machine was a Boy 35 E VH, with a clamping force of 35 tons. Shot size was 0.95 ounce for the nylon and 0.46 ounce for the LSR. Cycle time was 58 seconds.
Ron Shinn, editor
Contact:
Boy Machines Inc., 610-363-9121, www.boymachines.com
Ron Shinn | Editor
Editor Ron Shinn is a co-founder of Plastics Machinery & Manufacturing and has been covering the plastics industry for more than 35 years. He leads the editorial team, directs coverage and sets the editorial calendar. He also writes features, including the Talking Points column and On the Factory Floor, and covers recycling and sustainability for PMM and Plastics Recycling.
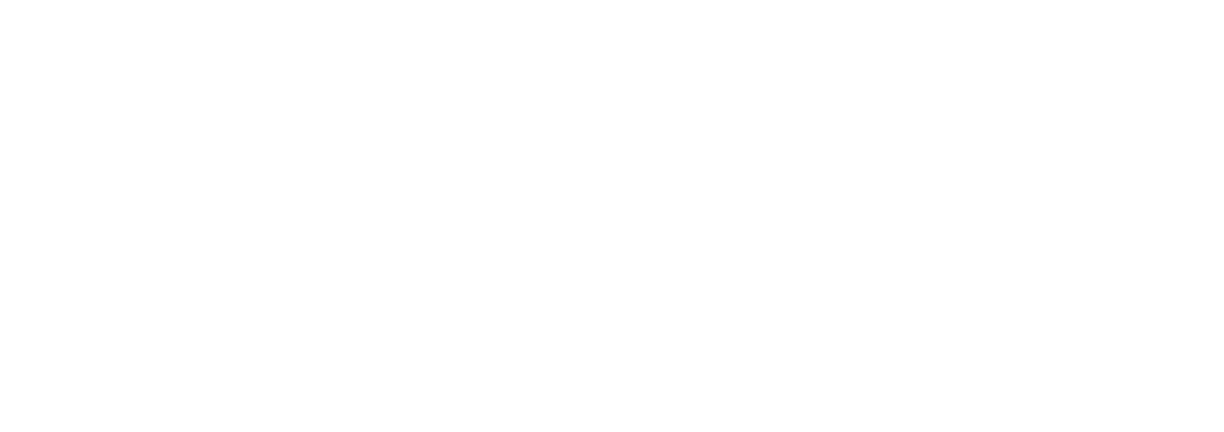