Quicker installation and overall ease of use are the themes for companies that manufacture heating or cooling components or insulating products for injection molding machines.
Barrel heating is a relatively straightforward process in injection molding, but heater manufacturers are constantly on the lookout for ways to enhance their products.
Tad McGwire, president of Industrial Heater Corp., Cheshire, Conn., provides some insight into matching the best heater to the need. His company makes band heaters for industrial processing.
Mica bands are preferred in situations that have the potential for contamination and require high watt densities — the wattage per square inch of surface area, he says. The typical range for mica bands is 25 to 45 watts per square inch. Some of the newer mica styles include mica that has higher temperature capabilities and can be rated as high as 70 watts per square inch. Mica bands, particularly high-watt-density bands, must make complete contact with the surface being heated; otherwise, they overheat and are damaged.
Ceramic is preferred where higher operating temperatures are required, or where energy-efficiency and reduced operating expense are important, he says. Ceramic bands can reach temperatures of 1,400 degrees Fahrenheit. The standard ceramic band is manufactured with an integrated insulation blanket that significantly reduces heat loss. Ceramic bands are also more forgiving during installation as they are completely flexible and operate both as conductive and radiant heaters.
With regard to placement, mica bands typically are narrower than ceramic, are spaced evenly across the width of the barrel and cover roughly 70 percent of the surface area. Three to four heaters per zone are ideal for wiring purposes. Each heater can be manufactured to work in lower voltage, single-phase applications and then wired individually. It can also be wired for three-phase, 480-volt applications. Due to the built-in energy-efficiency of ceramic bands, they tend to be wider and, in most cases, are installed one to two heaters per zone.
Industrial Heater has developed the new Mica FT Band Heater, with the "FT" standing for flexible and thin. The heater was designed for rapid installation and maximized thermal transfer. The quick-release latches eliminate the need for hand tools during installation. Tightening also is needed after the first heat-up.
When energized, any heater first heats itself and then conducts heat to the barrel. The FT heater has less mass to heat and therefore transmits more energy into the process. The FT heater is manufactured with a high-grade mica and is capable of watt densities up to 70 watts per square inch.
The edges of the heater are rolled to the inside diameter, helping to seal the element from any contamination. While not contamination-proof, it is more contamination-resistant than standard mica bands.
Industrial Heater also recently introduced radiant heat panels, which can be made with either mica-insulated emitter strips or tubular heaters. The panels can be easily installed with either standard or custom-mounting brackets and easily repaired, as the emitters are readily replaced.
IMPROVING HEATER BANDS
Tempco Electric Heater Corp., Wood Dale, Ill., makes customized bands. The company began making mica bands and then expanded into different types to include mineral-insulated, ceramic, tubular heaters, as well as a maxi-band heater that is aluminum with tubular elements in it. It also offers cast-in heaters. These are aluminum and bronze heaters used in plastics processing.
"We've added them over time and made them to the needs or wants of the customers to meet different type of challenges," says William Kilberry, VP of sales.
Recent improvements to Tempco's bands have included additions to its mica bands and ceramic bands. On its Duraband brand of mica band, Tempco has added easily removable abrasion protection over band heaters that have wire leads. This makes the abrasion protection removable so that it can be reused. It also has a new configuration on the ceramic bands that improves handling and mounting. This is designed with interlocking bricks that allow easier installation. It will be offered soon following a soft launch.
INCREASING PRODUCT OFFERING AT IMS
At IMS Co., Chagrin Falls, Ohio, officials have seen a recent increase in requests for customized heaters of all sizes and shapes. This has included everything from flat-strip heaters to circular heater bands with custom cut-outs and thermocouple holes, flexible ceramic barrel bands, rectangular die heaters for extrusion-type plastic processing, and aluminum- and bronze-cast heaters with built-in water passages.
The company, which is a distributor, also now stocks many coil heaters for hot-runner injection molding applications. Built-in thermocouples are available, says Steve Lortie, technical sales and service product specialist.
Heater capabilities constantly are being improved and expanded at IMS, specifically because of the increased use of engineered resins, and the higher melt temperatures they require, he says.
An example of such a product is the higher wattage Hot Sleeves Xtreme bands. These are high-temperature mica-insulated bands that are capable of twice the watt density of a standard mica nozzle heater. IMS now offers these as small as 1-inch diameter by 1-inch wide and up to 8 inches in diameter in both 120 and 240 volts.
INSULATION PRODUCTS STABILIZE, RETAIN HEAT BUT ALSO QUICKLY COOL
Insulation systems from UniTherm International Inc., Lewisville, Texas, are undergoing a transition, the company reports.
The UniVest product line now is offered in standard sizes as of earlier this year, says company spokeswoman Kendal White. It is finding applications even beyond injection molding barrel insulation, which was its original purpose. UniVest is a removable and reusable insulation jacket that can withstand temperatures up to 1,200 degrees Fahrenheit. It has a polytetrafluoroethylene-coated exterior and high-temperature strap-and-buckle fastening system.
UniTherm also is in the process of standardizing its QuickCool product line. An extension of UniVest, it is offered as a custom-engineered solution. White says custom molders need the ability to cool machinery rapidly because of the many tool changes they need to make.
UniTherm uses a concrete example to illustrate the savings potential. A 500-ton injection molding machine costs $622 to insulate. The machine operates 24 hours a day, five days a week throughout the year. The return on investment is 6.54 months for this machine, with an average of $95.18 savings per month and an average of $1,142.16 savings per year.
Merle R. Snyder, senior correspondent
Contact:
IMS Co., 440-543-1615, www.imscompany.com
Industrial Heater Corp., 203-250-0500, www.industrialheater.com
Tempco Electric Heater Corp., 630-350-2252, www.tempco.com
UniTherm International Inc., 972-436-1401, www.unitherm.com
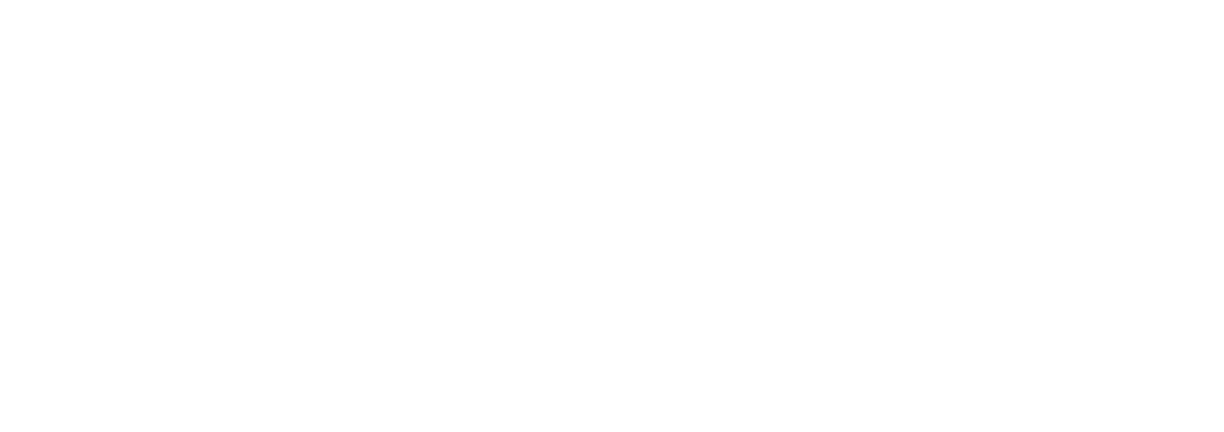