Let's say you have a fleet of standard, single-material injection molding machines and now have a job waiting for you if only you had two-material capability. The request comes from an established customer you don't want to lose. You're stuck, right? You have to invest in a new machine with two-material capability. Not so fast. There are options to get the job done.
Among the options are the E-Multi products from Milacron Plastics Machinery America, Batavia, Ohio; the Universal Multishot Systems (UMS) from MGS Mfg. Group Inc., Germantown, Wis.; and the Twinshot system from Nordson Xaloy Inc., New Castle, Pa.
MILACRON BUILDS ON CO-INJECTION ACQUISITIONS
Milacron has been active in acquiring co-injection technology over the last few years, buying E-Multi supplier Mold-Masters, Georgetown, Ontario, and Kortec Inc., now known as Milacron Co-injection. It offers Co-Injection Connect, a suite of services, including consulting, for clients interested in co-injection technology. In September, the company announced numerous enhancements to the four models of its E-Multi auxiliary injection unit line, the EM1 and EM2 and the larger EM3 and EM4.
The overall range offers screws from 14 to 25 mm, and the models can operate alongside a Milacron injection molding machine or be used with other brands, says Yann Coquelle, E-Multi global product manager. All four models use servomotor drives and can be designed to be mounted on either the mold or the platen. They come with a wide range of integrated options, including a variety of valve-gate controls, servo mold functions and temperature controls.
The mold-mounted E-Multi EM1 has a new carriage for compact fit into the molding area. It also has increased nozzle protrusion adjustment from plus or minus 5mm to plus or minus 15mm, as well as greater tie-bar clearance, thanks to a relocation of the spring pack, a device that maintains nozzle contact force when the actuator is powered off. In addition, as an option for applications requiring sprue break (the ability to retract the nozzle away from the melt inlet), mold-mounted EM1 and EM2 units are available with servo carriages. This allows them to be used for applications in which the melt inlet moves relative to where the secondary injection unit is located, or in applications that require injection at the parting line.
A new optional feature is available for the EM3 and EM4 models. The two models can now be outfitted with E-Multi Radial. The radial unit, which mounts on the top of the stationary platen, provides unobstructed access to the mold-mounting face for quick mold changes. On these models, servo sprue break motion is standard. The EM3 and EM4 units are capable of shots of between about 2 ounces and 17 ounces, the company says.
In addition to making physical enhancements to the E-Multi units, Milacron has also upgraded its E-Multi software. The upgrade, Version 1.34, has 68 new features and enhancements. It allows users to integrate E-Multi systems with a Milacron Varian rotary table, which can be used to rotate the mold for multishot applications, if needed. Table integration also makes it easier for users to set up the system. Other new features include automatic carriage calibration and safety ramp control for high-speed injection.
MGS ADD-ON FOR CLEAN-ROOM APPLICATION
MGS offers its UMS portable servo and hydraulic injection units in horizontal, vertical and mold-mounted options to accommodate differing shot sizes, ceiling heights and floor space requirements. In addition to selling many standard sizes, the company builds custom units.
For an OEM brand owner in the medical and pharmaceutical industries, MGS customized a UMS unit, the E14M. It is installed on a 550-ton Arburg Allrounder 920 A injection molding machine in an ISO Class 8 clean room. The servo injection unit is mounted directly onto the injection mold and uses a 14mm screw to deliver a second shot, in this case a thermoplastic elastomer (TPE), to a two-material common-core mold configured for multiple shots. The end product is used for medical diagnostic procedures.
The customized UMS unit incorporates pneumatic valve-gate control and a vibratory-assist option that orients the pellets to control how densely they are packed together, allowing for optimal processing. The system includes control of both the servo rotary motion of the installed MGS turntable and the coining in the mold. Coining refers to a controlled movement of a steel insert in the mold to compress a specific area of the part during packing. This is to achieve precision tolerances in specific areas.
MGS Mfg. Group's John Berg, director of marketing, says the applications for the technology continue to expand. In particular, health-care product molders have increasingly used the technology.
XALOY OFFERS TWINSHOT
Nordson Xaloy describes Twinshot as a multi-material molding system with a single-injection unit designed for easy retrofitting to injection molding machines. With Twinshot, a conventional machine with a single barrel and screw can inject two materials in one operation, with one material totally enclosing the other.
Volume is controlled by varying primary or auger feeder screw speeds to produce a three-layer construction. Two independent melting sections are used, one for the skin material and the other for the core material with multizone temperature control.
In the single-shot mold-fill system, the first part of the shot is skin; the second part is core. The skin material fills the outer geometry of the part and cools as the inner material flows through the interior. The system removes cost barriers to performing multicolor or multimaterial molding, allowing molders with single-material machines to add these processes at a manageable cost, regardless of machine brand.
Merle R. Snyder, senior correspondent
Contact:
MGS Mfg. Group Inc., 262-255-5790, www.mgstech.com
Milacron Plastics Machinery America, 513-536-2000, www.milacron.com
Nordson Xaloy Inc., 800-816-7711, www.nordsonpolymerprocessing.com
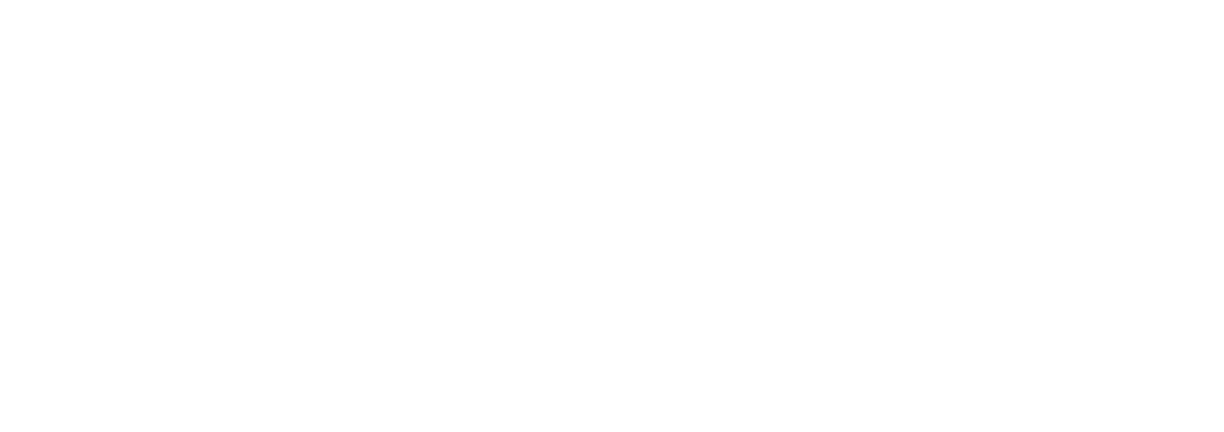