Dustin Kremer thinks he can shake up the North American extruder market by using extruder design principles and manufacturing techniques he has honed building machines in China for the past four years.
Kremer owns 50 percent of Shanghai Uway Plasmec LLC, which has two plants in China. He and business partner Will Wood started the company four years ago, and in 2014 manufactured 64 sheet lines and about 130 twin-screw extruders. Now Kremer is launching Uway Extrusion LLC in Warren, Ohio, to build the same types of machines for the North American and European markets. Kremer is the sole owner of the U.S. company.
"We were trying to build high-end machines in China for the North American market, but there were just too many production delays," he said in a recent interview. Delays came from shipping key components from the U.S. and Europe to China, then shipping the finished extruder back to the U.S. "It just didn't make much sense."
Kremer defined high-end extruders as machines that can process more than 1,500 pounds of material per hour.
The Ohio plant initially will focus on two products. One machine will compound directly to an extrusion line and the other will make sheet from 0.008 to 0.5 inches thick. Kremer expects to build three machines this year and about 10 next year.
The automotive industry, with its large appetite for sound-deadening components, will drive the compound-to-direct extrusion market. Instead of buying compounded pellets and putting them through a single-screw extruder to make a product, Kremer said the manufacturer can save 40-60 percent of the cost of a part by switching to direct compounding.
The Uway system uses multiple components to dose and blend the material, then feed it into a twin-screw extruder.
"The twin-screw machine will mix the components well," Kremer said. "We use a long screw in a big-diameter barrel and run it at a low rpm so it does not put much shear into the material. The key is low rpm.
"A lot of extruders have short screws and run at high rpm," he said. "Those are the wrong things to do for direct-to-sheet extrusion. We have had good success in Europe because our machines reduce shear and make the material more resilient."
At the end of the compounding extruder, the material goes into an accumulator. Next, it goes into a sheet die and then on to calendaring. To generate enough pressure to spread the material evenly across the die, Uway uses a single-screw extruder running at about 30 rpm instead of a melt pump. Kremer says melt pumps can add even more shear to the material.
Uway extruders built in Ohio will have frames, blowers and heaters from China. Other components will come from the U.S. and Europe, including gearboxes from Zambello Riduttori Srl, Magnago, Italy; screws and barrels designed and manufactured by Tim Womer at TWWomer & Associates, Edinburg, Pa.; motors from Weg Electric Corp., Duluth, Ga.; electrical components from Schneider Electric, Rueil-Malmaison, France; and drivers from ABB Ltd., Zurich.
"We try to keep our designs simple for all the machines we build," Kremer said. "Everything is easy to open and get access for maintenance.
"But we are a custom machine builder and some customers need a machine to fit the space they have," he said. "We will design a machine to fit just about any space that is available."
The heavy-gauge sheet systems Uway plans to build in the new plant will offer a higher throughput than comparable machines on the market today, Kremer said. He says each machine will be designed so that it can be modified in the processing plant as the user's needs change.
Kremer says he also plans to stock barrels and screws that can be delivered to customers in two weeks, a much shorter time than most suppliers need for replacement orders.
Ron Shinn, editor
Contact:
Uway Extrusion LLC, 765-592-6089, www.uwayextrusion.com
Ron Shinn | Editor
Editor Ron Shinn is a co-founder of Plastics Machinery & Manufacturing and has been covering the plastics industry for more than 35 years. He leads the editorial team, directs coverage and sets the editorial calendar. He also writes features, including the Talking Points column and On the Factory Floor, and covers recycling and sustainability for PMM and Plastics Recycling.
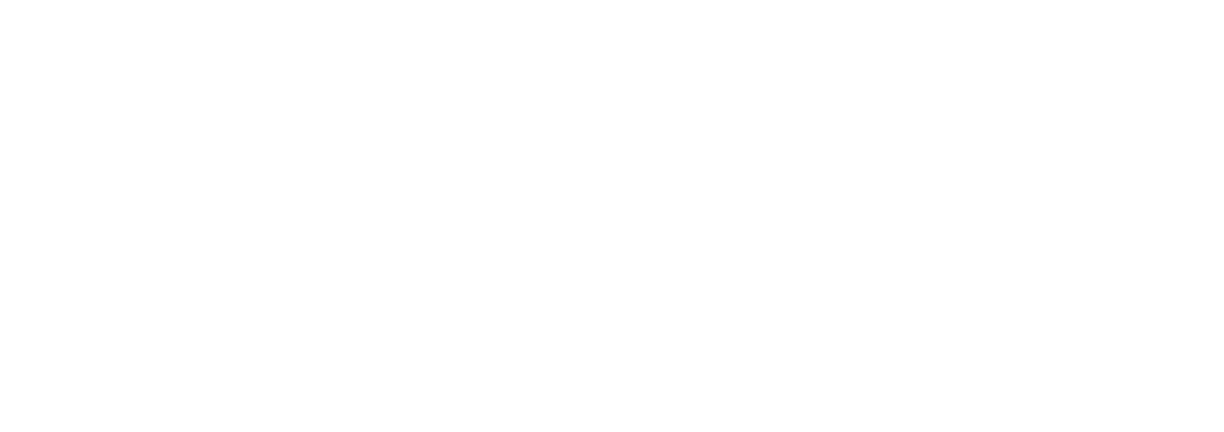