New foam injection molding process uses 'breathing mold' technology
A new potential entry in high-volume composite manufacturing represents a shift in foam injection molding.
The developmental foam injection molding technique incorporates a controlled mold movement during processing. It uses integral foams reinforced with long glass fiber that are suited to industrial or automotive projects.
The not-yet-commercialized, one-shot sandwich technique was introduced at Molding 2015 held in Rosemont, Ill., in June. Marcel Holzner, research engineer at the Fraunhofer Project Centre for Composites Research at Western University, London, Ontario, made the presentation.
The report, "Investigations on Injection Molded, Long-Glass-Fiber Reinforced Integral Foams Using Breathing Mold technology," says the technique has the potential to increase the overall thickness of parts; allow foaming in specific areas in a part requiring properties such as high flexural stiffness; and produce parts with areas of strikingly different densities.
WHY GO THIS ROUTE?
The technique involves the use of materials reinforced with long glass fiber that are combined with foaming. It calls for the mold to open during part forming. The process brings weight savings and dimensional stability and increases flexural rigidity of a part by several hundred percent without embrittlement (loss of ductility) during foaming. Materials such as nylon 6 or PP with up to 50 percent long glass fiber are being tested for properties like bending stiffness, embrittlement and lightweighting potential. Potential industrial applications include dashboard carriers for BMW and soft-touch surface parts for Mercedes-Benz, where they could provide additional weight reduction, says Holzner.
The Fraunhofer Project Centre is a joint venture between Western University and Fraunhofer Institute for Chemical Technology in Pfinztal, Germany. The study at the project center applies the part-foaming step in a manner different from conventional techniques. With this process, the mold is partially filled in a short-shot injection step that lets the foaming action expand the part, filling the void.
In the foam injection technique being tested at the Fraunhofer Project Centre, the gas-loaded fiber-reinforced polymer fills the entire cavity. As the mold opens, the pressure drops and foaming begins. Varying the time delay of the mold opening movement following mold fill allows the processor to tailor the thickness of the skin layer.
"You can choose different opening strokes for the mold, starting at 2 millimeters and opening to 4 millimeters, or starting at 5 millimeters and opening to 12 millimeters. The technique is quite an old idea, but here in this study we wanted to investigate the lightweighting potential of this technology, how it can decrease the density of the final part and evaluate [it] by mechanical properties," says Holzner.
HOW THE MOLD MOVES
The mold movement is carried out by actuating the platen and not through a specialized movement in the tool. This allows for standard tools to be used. A standard clamping unit also can be used; however, the clamp opening stroke is controlled through the addition of special regulators, says Holzner. They're positioned on the back of each clamping column to provide additional parallelism control for precise opening of the mold.
With the primary machine's software, workers can set delay time and opening stroke and speed.
The Fraunhofer Project Centre is testing its breathing-mold approach in several configurations, including a standard injection unit with a low-shear screw for processing of long-fiber-reinforced resin. For foaming, a chemical blowing agent is used.
The center is conducting tests using a MuCell standard injection screw and a new MuCell long-fiber screw design for low-shear processing. MuCell is comprised of a supercritical fluid gas-dosing unit and a screw design featuring non-return valves and a fiber-preserving gas-mixing zone. This configuration processes the long-glass fibers more gently while foaming with MuCell.
Two non-return valves are installed on a screw for a MuCell application; higher pressure is generated in the screw section in between these two valves where the gas dissolves into the polymer.
The new screw, in testing for two months, features design changes to the second non-return valve and the gas-mixing zone of the screw to provide larger gaps where the fibers can pass through with minimal damage. The Fraunhofer Project Centre is running its tests on a KraussMaffei KM 1,600/12,000/4,300 MX L hydraulic injection press with 1,760 tons of clamping force.
The test mold used was not designed specifically for this process, which indicates that standard or existing tools may be used when the project is proven and moves into a commercial stage. The project center processes material containing glass fibers 12mm long. It does so to manufacture parts strong enough for automotive applications, but also to study how the process impacts fiber length.
Mechanical testing and fiber length measurements are not finished yet.
ADVANTAGES OF NOTE
• The skin layer of the part is more uniform over the entire part when foaming starts with a full cavity — a short-shot injection step can yield a thicker skin layer at the injection point and a thinner skin layer at the end of flow path, says Holzner.
• Lightweighting and more foaming. Holzner molded a test plaque in a short-shot step, yielding a part weight reduction from 8 to 10 percent. The breathing-mold approach yielded part weight reduction of 20 to 25 percent.
• The density and viscosity reduction provided by bringing nitrogen or carbon dioxide to a supercritical state for physical foaming achieved in the MuCell process reduces required process temperature, clamping force and energy consumption. Density and viscosity reduction also is possible with a chemical blowing agent. The viscosity reduction of gas-loaded polymers is compared to unloaded polymers.
• MuCell helps the breathing-mold approach because more gas dissolves into the polymer, unlike a chemical blowing agent where the gas can disappear at the end of the injection machine and through the hopper. The ability of MuCell to greatly reduce density can be coupled with the breathing- mold process to make a larger and lighter part.
Mikell Knights, senior correspondent
Contact:
Fraunhofer Project Centre for Composites Research, 519-661-3150, www.eng.uwo.ca/fraunhofer
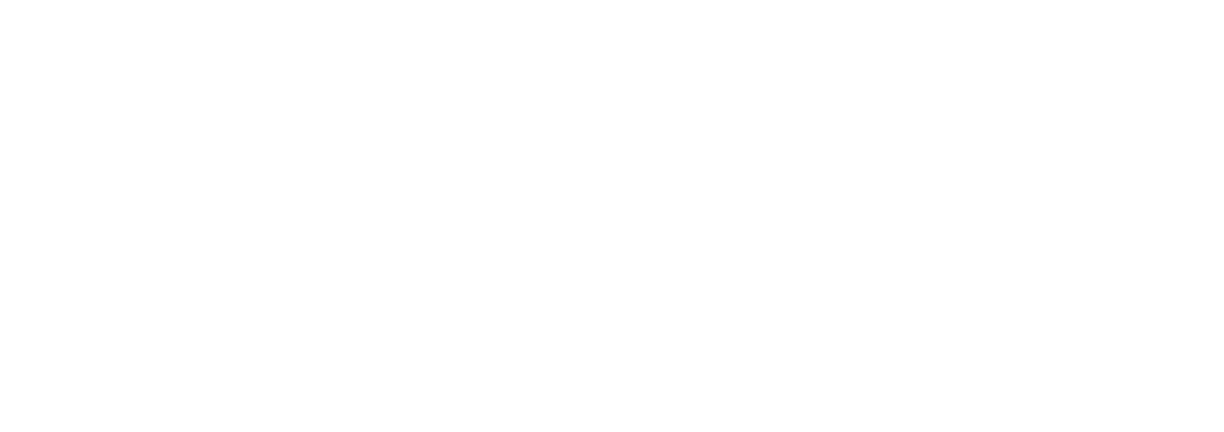