Ultrasonic welding has come a long way since it was considered merely a way to make things stick together when other methods were inadequate. Demanding applications requiring sophisticated controls have become the norm, making welding a high-end process.
Examples from two leading suppliers of ultrasonic welding equipment, Dukane Corp., St. Charles, Ill., and Branson Ultrasonics Corp., Danbury, Conn., illustrate the new capabilities.
A medical device manufacturer in the Midwest, which has asked not to be identified, uses Dukane's iQ Series servo ultrasonic welding system to assemble small, delicate cholesterol test strips. The strips are made of two thin layers of PET film surrounding a mesh membrane infused with a reactive chemical. Manufacturing them requires precise welding control.
Prior to employing Dukane's iQ technology, the strip manufacturer had challenges involving the misalignment of the PET film. Since adopting the iQ Series' digital process control, the company has produced more than 20 million test strip assemblies in less than three years while reducing its scrap rate from 30 percent to less than 5 percent.
According to Mike Luehr, applications technology manager for the Dukane Intelligent Assembly Solutions division, the process involves multiple parameters that can be set when defining the weld- cycle sequence. To make the test strips, the system is programmed to trigger the weld cycle using minimal force. As each weld cycle is initiated, the ultrasonic horn descends towards the assembly rapidly. Approximately 1mm above the assembly, the horn slows down to a programmed speed. Then the Melt-Match feature is initiated. When the system reaches the programmed trigger force value on the test strip, the horn's downward movement stops and the controls initiate vibration of the horn to soften the film. Next, the system's load cell detects a programmed drop in force, indicating the film has begun to melt. At that point, the weld-cycle's downward motion re-initiates to further compress the film.
Welding continues to a programmed distance or energy value. The Melt-Detect feature prevents unnecessary force on the thin film that could distort it.
The iQ servo system also gives flexibility to provide dynamic and/or static hold. With dynamic hold, the horn can further compress the parts after the ultrasonic horn has been turned off. Using static hold, the weld horn holds its final end-of-weld position for a set time.
In the test-strip application, static hold has been programmed. This gives the materials enough time to solidify without misalignment. Once the static hold time has been completed, the horn then returns to its home position, ready for the next weld cycle.
An advantage of using the iQ servo system is the ability to duplicate a known process on multiple systems without any variation in weld results. This was a major benefit for the test-strip manufacturing company, which was able to install multiple systems without investing extra time or effort in fine-tuning the process for each welder.
PRECISION HORN MODIFICATIONS
SOLVE SEAL PROBLEM
Branson cites an example in which it helped get an automated production line back into operation by solving a critical plastic joining problem.
The background is this: Blendtec Inc., Orem, Utah, produces a blender which, unlike most blenders that operate at a few thousand rpm, operates at 28,000 rpm and is known for its ability to pulverize virtually any material, not just the fruits and vegetables for which blenders are often used.
One detail of the blender is the blade-bearing drive assembly that is hermetically sealed to the bottom ring of the blender jar. This design feature results in high durability, making possible the company's eight-year warranty.
To meet increasing demand, Blendtec decided to fully automate one of its production lines. For help, it contacted Branson, which determined a Branson 2000X ultrasonic assembly system with robotic feed would meet the needs of the situation.
The challenge came when Blendtec, in its ongoing quest to improve performance and quality, decided to redesign its blender jar by increasing the diameter of the lower seal. What the company did not realize was that changing the diameter size would affect the integrity of the hermetic seal.
Already fully committed to the new container design, and gearing up to fill a large order, Blendtec discovered that the Branson ultrasonic horns that had functioned properly using the old container design were now too tight. The welds were failing internal quality testing. Production came to a halt.
"Branson was able to respond immediately," says Tim Herren, Branson western regional manager. Branson's evaluation determined that the horns needed to be modified to properly seal the new container design. Branson engineers went to work making the modifications and programming new weld parameters. The seal was once again hermetic.
"Branson made the fine-tuned adjustments to the horn redesign, and we were back into production," says Brad Hanson, Blendtec's manufacturing engineering manager. He says the welder "took the horns that had become useless because of our redesign and remachined and retuned them so we can reuse them in the future."
As a result of Branson's modification of the horns and weld parameters, Blendtec achieved the weld joint it needed and returned to full production within hours. It also met the critical shipment deadline that had been in jeopardy.
In addition to solving the joining problem, Branson made adjustments so Blendtec could take advantage of the precise weld-by-energy feature on the Branson 2000X. Welding by energy rather than by time provides an added quality-assurance checkpoint and safeguard for weld strength.
Merle R. Snyder, senior correspondent
Contact:
Branson Ultrasonics Corp., 203-796-0400, www.emersonindustrial/en-US/branson.com
Dukane Corp., 630-797-4900, www.dukane.com/us/
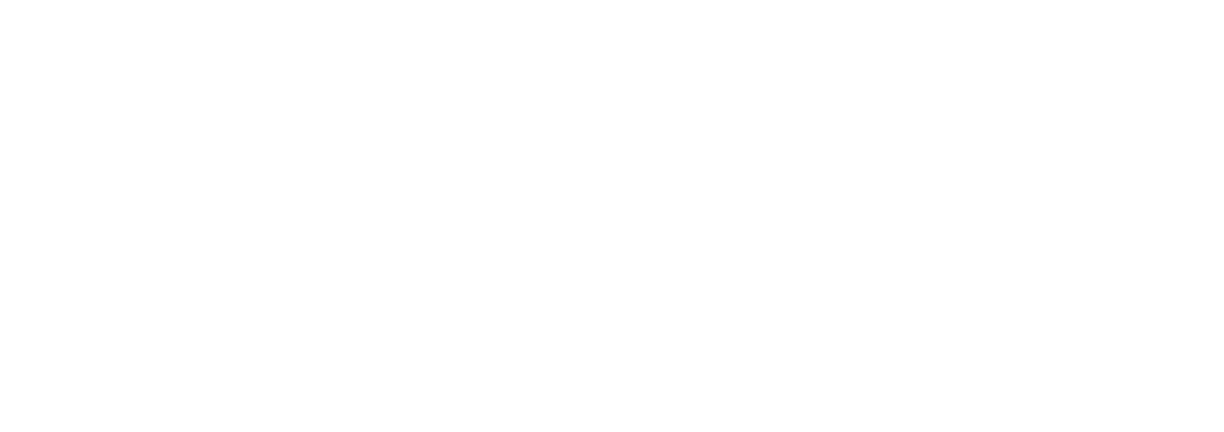