The Society of the Plastics Industry released a risk assessment report for injection molding machines focusing on the necessity of having a mechanical device (a drop bar, jam bar, ratchet bar or friction-type device) in place to prevent the unintentional and unexpected closing of platens to avoid possible injury to personnel. (Please review feature story on safety from April 2015).
This mechanical device is not required under European safety standard EN 201 since that standard was revised in 2009.
The report, commissioned by the SPI Equipment Council in 2014, is an effort to further harmonize machine safety standards between North America and Europe. It was conducted by Design Safety Engineering Inc., Ann Arbor, Mich., to evaluate whether the mold closure prevention device, specified and required in the B151 standards developed by the American National Standards Institute (ANSI) and SPI, are needed.
"Any European machine coming to the U.S. must have a jam bar, and this has been a costly addition, according to machinery manufacturers," says Stan Glover, vice chair of the SPI Equipment Council and chair of the SPI Machinery Safety Standards Committee. The industry has been unable to establish a formal risk assessment of the mechanical device, so the SPI Equipment Council funded this independent, third-party test. The testing took place at the facility of Medbio Inc., a processor in Grand Rapids, Mich., which allowed evaluations on its horizontal and vertical machines.
OSHA does not perform standards development but creates rules and regulations that impact the industry (see PMM April 2015 story). In case of an accident OSHA would cite relevant standards.
The report was released at NPE.
CURRENT HORIZONTAL MACHINE
DESIGNS CAN DROP THE JAM BAR
According to the report, from a technical risk-assessment perspective, the mechanical device provides "redundant redundancy" on horizontal injection molding machines that are designed and constructed in accordance with the B151.1-2007 standard.
"The mechanical device provides no additional risk reduction beyond that provided by the electrical and hydraulic control systems for foreseeable failures that could result in unexpected motion," reads the report.
The report also states that horizontal injection machines that have safety-related control systems in place that meet the requirements of the Type III interlocks in the B151.1 standard for PLC control systems in ISO 13849-1 provide an acceptable level of risk reduction.
"Based on the risk assessment of the horizontal injection molding machines, the requirements for the mechanical device for this configuration of injection molding machine can be removed from the B151.1 standard," reads the report.
However, the report also determined that on vertical, inclined or hybrid injection molding machines, the mechanical device, required by ANSI/SPI B151.29 for vertical injection molding machines, "may provide additional protection by preventing the closure of the platens due to gravity, when the control systems are inoperable."
The conclusion of the report does not apply to older machines unless the safety-related control systems meet the current standards. Furthermore, "the presence or absence of a mechanical device does not relieve machinery users from following proper lockout/tagout procedures for tasks that require lockout," says the report.
WHAT IS NEXT FOR MACHINERY SUPPLIERS
Machinery suppliers and processors have to conduct their own internal safety assessments to determine for themselves whether they want to remove the mechanical device or not, says Glover.
"It is fair to say that there is additional work to do regarding the legal landscape of the jam bar, especially in Michigan," he says. OSHA in Michigan has a measure in place calling for use of it. The device also is recognized by OSHA on the federal level.
SPI is the ANSI-accredited developer of American National Standards for plastics-related machinery in the United States. Volunteers from SPI member companies, comprised of plastics processing or machinery makers, are on committees that review the standards then write or revise them.
The SPI Equipment Council is composed of companies that manufacture machines, components, molds and auxiliary equipment. The Machinery Safety Standards Committee features subcommittees relating to a given plastics manufacturing process. Glover is also the U.S. TAG Chairman to the International Organization for Standardization (ISO) Technical Committee 270 (TC 270) as well as to the TC 270 Working Group 1. The U.S. delegation, along with 11 other member countries, met in Munich in April to continue development of a new global ISO-based safety standard for horizontal and vertical injection molding machines.
"In the U.S., our safety standards are not only about the safety of the machinery but the safe use of the machinery, unlike in Europe, where national labor laws address this aspect of user safety," says Glover. He says that having input from processors on standards development is paramount.
Standards that are established remain in place for 10 years, but revisions are considered after five years.
Mikell Knights, senior correspondent
Contact:
Society of the Plastics Industry, 202-974-5200, www.plasticsindustry.org
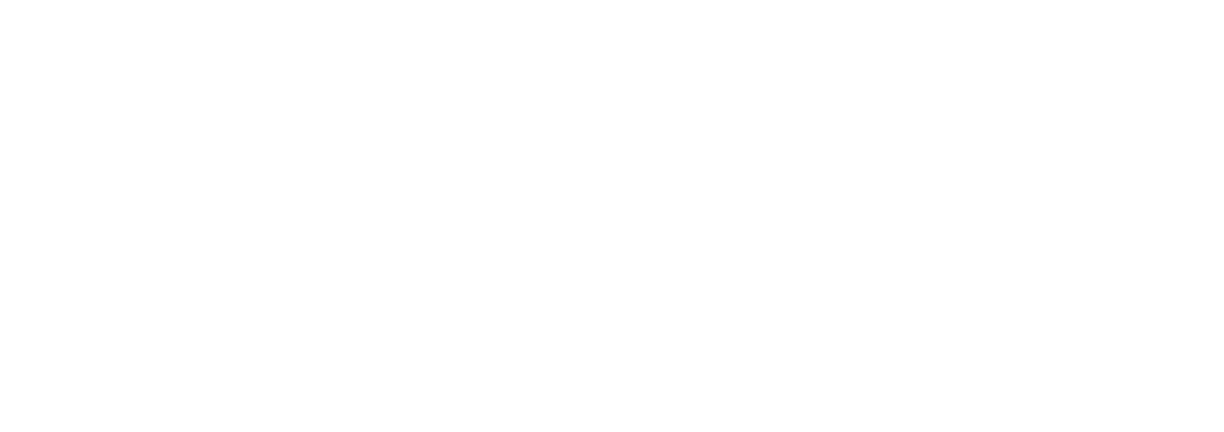