Special Report: Plastics machinery safety standards keep risks at a minumum
American National Standards Institute/SPI Plastics Machinery Safety Standards are available for purchase on the website of the Society of the Plastics Industry. During 2014, four newly revised standards were announced and a completely new standard for blow molding machinery replaced two previously separate standards for extrusion blow molding and injection blow molding. The revised standards are for extrusion machines, vertical clamp injection machines, plastics sheet production machinery and integration of robots with injection molding machines.
In the not-too-distant future, there will be one fewer of these American National Standards Institute (ANSI) standards when separate standards for horizontal and vertical injection molding machines are combined into a single new one, as they were for blow molding. That work is already underway.
SPI is the ANSI-accredited developer of American National Standards for plastics-related machinery in the U.S. ANSI has a 10-year cycle on these standards; at five years SPI has to start revisions. The actual writing of the new or revised standard is done by a committee of volunteers from SPI member companies, each with expertise in injection molding, blow molding, extrusion or robotics. They meet, on average, twice a year and also have teleconferences between meetings. The revision or creation of a new standard is detailed and thorough, as is easily seen by a quick reading of the table of contents of one or more. The standard is a very useful tool for a processor.
Solid reasons to be current with safety standards
The paramount reason for having and following safety standards is obvious: the safety of every member of your team. That should be a given, but there are many more good reasons and buying yours is easy and inexpensive: between $46 and $75 at SPI's online Plastics Industry e-store.
The safety standards are a solid base for training employees, especially those who work directly with the machinery. Your insurance provider can tell you how important training is. It's also something OSHA will check into if there is an accident. The standards are a good guide to inspecting your facility for safety hazards.
Obviously these standards are not laws or court orders, and no one will come checking to see if you know them or are following them. But should an accident or other incident bring an OSHA staffer into your facility, he or she may not know an extrusion machine from a yogurt maker and is unlikely to have specific information on hand. That OSHA staffer will then search for the appropriate standards or technical guidance from other agencies and associations, including ANSI, according to SPI. Subsequently, the OSHA representative may ask you something like, "You're following this standard, aren't you?"
Standards enable proactive safety
When the new blow molding standard and the revised extrusion machine and vertical clamp injection molding standards were released in late March 2014, SPI said "substantive changes" had been made.
For example:
• Documented risk assessments are required from the machine manufacturer and the user.
• Definitions harmonized and standardized within the SPI portfolio of standards were added.
• Advances in safety-related controls, mechanisms and practices were incorporated.
• Extensive references for recommended safety procedures and circuits were provided in annexes.
• Existing machines were required to meet safety requirements, methods and signage of the 2014 standard.
Additionally, responsibilities have been assigned to the supplier, the remanufacturer, the modifier and the user to help with interpreting these requirements in all the standards.
Meet the standards makers, and be one
The Machinery Safety Standards Committee (MSSC), a primary component of SPI's Equipment Council, includes people from processors, equipment makers and end users, and its chair is Stan Glover, sales director of Zeiger Industries Inc., Canton, Ohio. There are four subcommittees, for injection molding, extrusion, blow molding and robotics. The SPI secretariat to the MSSC and the subcommittees consists of Katie Masterson and David Palmer.
Glover, in addition to being a very active chair of the MSSC, is also vice chair of the SPI Equipment Council and SPI's representative in the first International Organization for Standardization (ISO) Technical Committee Work Group (WG1), which is national Organization for Standardization (ISO) Technical Committee Work Group (WG1), which is in the process of developing an ISO safety standard for injection molding machines. There are 14 countries participating, including Japan, China, Turkey, Brazil and Switzerland, and five other countries observing. In April, Glover will be in Europe for a meeting of the WG1.
"The goal," says Glover, "is a uniform, global safety standard and the challenge is resolving regional and national issues." He adds that SPI has staff like no one else, a combination of diplomacy and technical expertise. All members of the MSSC are tech specialists as well, he says. "We have a few processors and we're striving for more," he says, "and they don't have to be SPI members. We need their particular input and feedback."
As chair of the Injection Molding Safety Standards Subcommittee, Jim Pilavdzic, manager of product safety at Husky Injection Molding Systems Ltd., Bolton, Ontario, is busy working to merge the two current injection molding standards for horizontal and vertical clamp machines into a new single standard. The group is a mix of machine and safety device makers, OEMs and users, he says. He wants more participants, though, from all links in the chain for their diverse points of view. "All points of view will be considered. Then we look for consensus," he says.
They are working on three areas where most injuries can occur: the mold area/clamp; purging, where very hot material under pressure comes out and has to be cleared; and the hopper area, where a number of things can cause a clog that needs a full-stop lockout to clear.
Pilavdzic strongly emphasizes training. Many processors have strict safety procedures, he says, but they are not ingrained into the operator, or a new operator comes in and goes straight to work.
Tom Limbrunner, senior VP applications and technology, and David Dorosa, VP engineering for sheet extrusion systems maker Processing Technologies International LLC (PTi), Aurora, Ill., got involved with the MSSC in 2008 and 2009 and have worked on two standards: extrusion machinery and sheet production machinery. Limbrunner recalls 10 or 12 people in early meetings and now 20 to 30 people are involved. Dorosa started in a November 2008 meeting by reviewing the existing extrusion machinery standard line by line, then bringing in new technology along the way. "It's not enforcement," he says, "but what the majority agrees is the right thing to do."
In general, says Dorosa, they identify every hazard they can — thermal, crush, etc. — then discuss each. Designing the hazard out upfront is the ideal, but if that's not possible, companies should provide guarding for protection; and, if risk still remains, use warnings, labels and, above all, training.
Limbrunner said the 1999 version of the sheet production standard had almost no illustrations. The new one has examples of guarding and more, making it much easier for someone to understand. "It's got a lot more meat," he says.
The new 2014 blow molding standard that combined and updated two previous standards was shepherded into being by the Blow Molding Safety Subcommittee, which Chuck Flammer of Kautex Machines Inc., North Branch, N.J., chairs. Noting that the standards are also aimed at machine makers, he says the subcommittee wanted to do risk analysis for machine builders but not tell them how to build it.
"We need to leave room to use new technology and designs," he says. "We identify an issue of risk and recommend an alarm or a block, for example. In the past, it was more like you had to have this and that.
"We want to follow more of a global standard so machines can be more easily distributed globally," Flammer says, as Europe is very safety conscious and goes farther on risk assessment and specific rules.
The safety standards makers are contributing in a major way to the betterment of the industry. For a processing shop that has had an accident, especially a serious one, the damage to the company's reputation and image only adds to the financial implications, and above all, to the impact on other employees' morale.
Others in the plastics industry should give serious consideration to helping advance the standards. Those doing it now want your point of view, particularly processors. There are two levels of participation. You can participate fully in standards development meetings, including the ISO standards meetings in Europe. Or you can participate in the review and commenting on working and committee drafts of developing standards.
Rob Neilley, senior correspondent
Current ANSI/SPI machine safety standards (March 2014):
ANSI/SPI B151.1-2007 Safety Requirements for Horizontal Injection Molding Machines
ANSI/SPI B151.7-2014 - Safety Requirements for Extrusion Machinery
ANSI/SPI B151.20-2013 - Safety Requirements for Plastic Sheet Production Machinery
ANSI/SPI B151.27-2013 - Safety Requirements for the Integration of Robots with Injection Molding Machines
ANSI/SPI B151.29-2014 - Safety Requirements for Vertical Clamp Injection Molding Machines
ANSI/SPI B151.31-2014 Safety Requirements for the Manufacture and Care of Blow Molding Machines
Links for more information:
SPI Machinery Safety Standards Committee homepage
http://www.plasticsindustry.org/IndustryGroups/IndustryDetail.cfm?ItemNumber=12386
ANSI/SPI Machinery Safety Standards (all) — view tables of contents
http://www.plasticsindustry.org/IndustryGroups/IndustryDetail.cfm?ItemNumber=12406
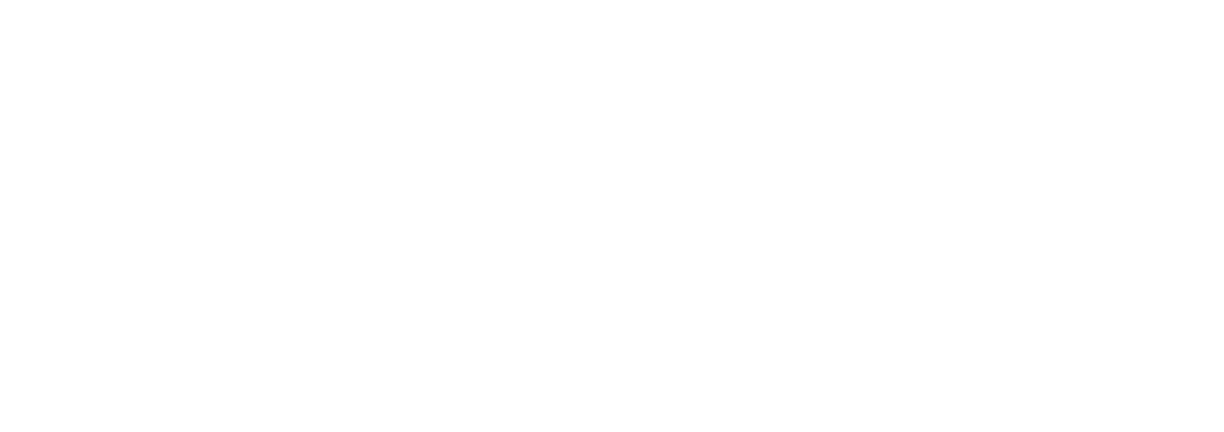