The U.S. plastics industry can expect to experience a steady infusion of auxiliary equipment technologies, Italian-style, as Universal Dynamics Inc., Woodbridge, Va., adapts technologies from parent company Piovan SpA and launches them stateside.
Acquired by Piovan in 2008, Una-Dyn has maintained its own identity and, where it makes sense, is adapting Piovan technologies for the U.S. market. During NPE, Una-Dyn showcased more than 10 new products, including brands AutoMate, Quantum, Lybra and EasyLink.
"These are items we're bringing to the market rather than developing them here," says Bill Goldfarb, president of Una-Dyn. "It's a technology exchange to bring to the U.S. these never-before-seen features that are successful in Europe. It's a two- or three-stage plan but items are delivered and integrated into our systems here, industrialized for the U.S. market with locally supplied components and controls, which builds up a ready support network."
AutoMate is one example. Piovan developed a multiple hopper central drying system that received its European patent in 2013. Marketed as Modula in Europe, the system is auto-adaptable with automatic control and adjustment of each hopper's process temperature and airflow. The entire system is controlled using Focus-pro control, which is Una-Dyn's touch screen control program.
Modula's big win has been its selection by BMW in Europe for making parts for the i Series vehicles, particularly the i3 and the i8. Auxiliary and primary equipment was selected based on consistency of production, energy efficiency and simplicity of use, such as maintenance requirements, scheduling of maintenance and human machine interfaces.
Components for those cars include co-injected molded hoods and triple injection molded bumpers and doors, all of which are produced by BMW.
"Based on the design of Modula, we've developed AutoMate in the U.S.," says Giorgio Santella, chief marketing officer with Piovan. Based on the size and scope of the U.S. automotive industry, Santella sees great potential.
"If we have this high degree of control that allows this constancy of production, the equipment is inevitably positioning itself at a higher level than other competitive products," says Santella. "If BMW has taken Modula, there must be a reason."
From an organizational point of view, all R&D takes place in Italy. That is then coordinated with the respective technical departments in each location. At Una-Dyn headquarters, officials are expanding the factory by 35,000 square feet to support local production. It currently has two buildings that together have 75,000 square feet of space. Una-Dyn is in the building approval process now, and expects the expansion to be completed in 18 months.
"It is normal practice for us to design a product over here and take that design and make it doable in the location where we want to produce the product," Santella said, emphasizing the need to adapt to local suppliers and regulations.
"Being adaptive to the U.S. market does not mean changing the design and performance of a product, but making it manufacturable in the U.S.," he says. "We give lots of emphasis to local production. In our programs all of those products seen at the NPE will one day be produced in the U.S. and be Una-Dyn branded."
Following on that strategy is the introduction of Quantum to North America. This is a gravimetric batch blender that was introduced at the K show in 2013. Two patents have been issued in Europe, one each on the dosing device and the mixing device.
The goal with Quantum was to introduce a gravimetric blender that had highly accurate dosing and more flexibility in terms of applications. The system is configured with controls that can self-adjust based on operating conditions. The blender is available in several configurations — Quantum 7 with a maximum throughput of 70 kilograms per hour (154 pounds) and the Quantum 12 with a maximum throughput of 120 kilograms per hour (265 pounds). In the applications where the plasticizing unit moves, the Quantum can be equipped with a remote mixer unit and installed beside the machine on a floor stand.
The system was designed to be mechanically and electronically isolated from vibrations and has an expandable configuration so that it can be expanded to three, four, five or six dosing stations by adding station modules.
The precision of dosing is increased by not using conventional slide gate dosing devices, says Santella. However, Piovan purposely focused on the mixer to ensure a homogenous blend. This can be particularly onerous with long-fiber granules, which are five to 10 times longer than a regular granule and have a cylindrical shape. Quantum can handle any possible raw granular resin, including virgin, masterbatch, regrind, reprocessed, long fiber, filled or any particular granulometry, shape and bulk density. Its new mixer has a spherical shape and circular paddle shaft for better homogenization of different materials with no risk of segregation or powder generation.
Santella says that dosing accuracy is extremely important but the industry focuses its energy on dosing without giving enough attention to mixing.
"Instead, with us, we put a lot of emphasis on the mixer," he says of the focus for the Quantum line. "You better have a homogenous blend."
Piovan has placed many units already, Santella said, with 200 to 300 installed in Europe. That includes installations where conventional blenders cannot be used.
Angie DeRosa, managing editor
Contact:
Universal Dynamics Inc.,
703-490-7000, www.unadyn.com
Piovan SpA,
39-041-05799111, www.piovan.com
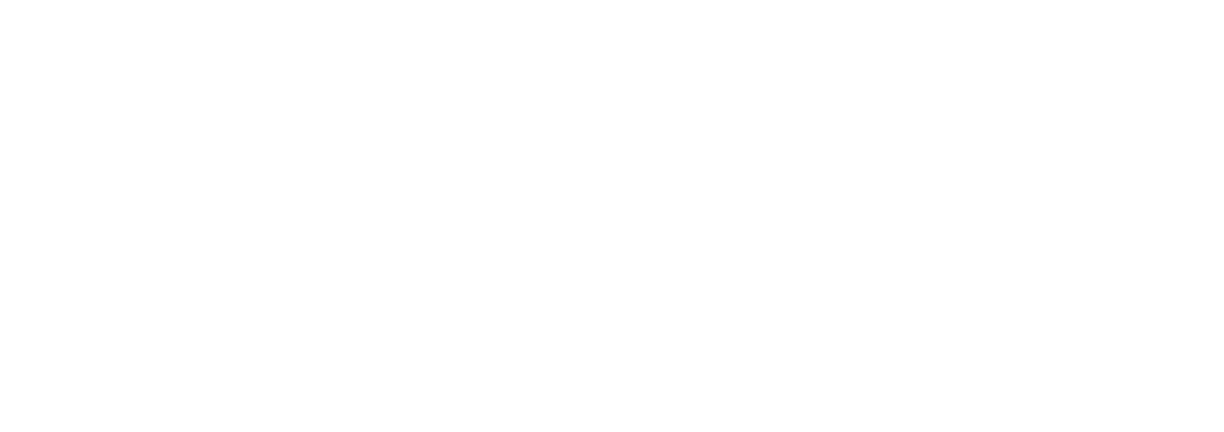