Vacuum brazing and laser sintering of mold inserts and tooling components that incorporate cooling channels are a conduit to improved injection molding cycle times.
Injection molding of parts where long cooling times can create a production bottleneck and uneven cooling can impact part quality are ideal candidates for mold designs that incorporate cooling channels that follow the contour of the part geometry.
Tooling with conformal cooling channels can contact mold sections unreachable with traditional straight-line gun-drilled channels, which can minimize hot spots, and prevent warpage and sink marks while lowering molded-in stress, improving part dimensional stability and part finish. Conformal cooling is finding greater use in parts where cooling time represents up to 70 percent of the total cycle time.
Demand for shorter cycle times with higher part quality has drawn U.S. molders with increasingly complex part geometries, more widely varying thin/thick wall sections and tighter tolerance segments that are hard to cool, to molds with conformal cooling. In the last two years, demand is also rising from molders of simple, flat or low-volume parts, where attaining a uniform surface temperature during molding is paramount. A conformal cooling conference held last September by Robert A. Beard & Associates Inc., Troy, Mich., covered the merits and facts about it for injection molding.
Officials from Linear Mold & Engineering Inc., Livonia, Mich., attended the conference. The company is a leading manufacturer of direct metal laser sintered (DMLS) tooling with conformal cooling channels in the U.S.
"The adoption of conformal cooling channels into mold cores, cavities, inserts and a growing range of tooling segments in order to mitigate hot spots and minimize cooling cycle times is gaining traction in North America," says Lou Young, director of new business development for Linear.
"There is a reshoring of the tooling industry; tools are coming back to the U.S., and processors need a competitive edge. More efficient tooling will vastly increase the market presence for tools with conformal cooling channels in the next year," says Andrew Snow, senior vice president at EOS of North America Inc., Novi, Mich.
Conformal cooling — an approach in which the cooling channels of the component are manufactured at the same time as the tool — is an alternative to traditional gun-drilled cooling channels or the use of mold inserts designed from highly conductive materials as a means of removing heat from the part.
Advocates of conformal cooling say the practice of gun-drilling straight water lines and using turn plugs at a channel direction change creates a low-turbulence area where sediment may build up, and cannot be used across the tool. Conductive inserts deliver increased heat transfer but may require higher upkeep and replacement as they may wear more quickly than a steel component.
Two toolmaking methods, vacuum brazing and DMLS, an additive manufacturing approach, leverage the design freedom and cycle time savings offered through conformal cooling channels. Two companies involved with the tooling technology, Polyshot Hot Runner Systems, West Henrietta, N.Y., and EOS of North America, say business has grown in the past two years.
RISE OF VACUUM-BRAZED INSERTS
Polyshot, a manufacturer of hot runner manifold systems and nozzle valve gates, gained its expertise with vacuum brazing during the last decade with the manufacture of such manifolds with improved flow paths. For the last seven years it has applied that expertise in the production of vacuum-brazed hot runner systems.
"Straight manifold channels made with drills and turn plugs turned at 90-degree angles cause holdup areas. Crossing the flow path of the cooling channel with a heating element results in different steel temperatures near the heater, causing a hot spot," says Doug Hepler, president and CEO at Polyshot. During the last two years, Polyshot has started to braze cores and cavities for molders and mold makers using its plate fusion technology, and has grown this work into more than 5 percent of its business.
Vacuum brazing starts with round or square steel stock that is sliced in a layer or layers. The flow paths for the water lines are cut with a CNC machine and the mating flat surfaces ground to finish. Polyshot fuses and assembles the block into a single piece in a proprietary high negative pressure vacuum-brazing operation. The flow paths are buried into the steel. The processor machines away the exterior of the steel block to produce a finished core or cavity after brazing.
Polyshot's first vacuum-brazed tooling insert was a core for an M16 clip mold presented by a molder that could only get cooling into the bottom third of the curved part due to the way the mold opened and rotated. Even with aluminum fixtures, cooling time amounted to 90 seconds.
Cooling channels with sweeping curves coursing strategically throughout the part trimmed the cooling cycle to 35 seconds.
"The part pops out with no bow, no issues," says Hepler.
More common applications include an ejector core for a stripper plate mold, manufactured with a conformal cooling channel that enters the insert, rises to several levels and wraps back and forth in a
serpentine fashion on each level before exiting the tool, trimming cycle time up to 60 percent. The insert with multiple levels, like the manifold, can be produced from several plates, aligned with dowel pins before vacuum brazing with Polyshot's plate fusion technology.
The vacuum-brazed ejector core insert with conformal cooling channels reduced the contact surface of the tool at the end of injection 70 degrees Fahrenheit. "If we have a mold with a 3.1-second cooling cycle and 10-second overall cycle and we cut the cooling time to 1.9 seconds and overall cycle time to 8 seconds that saves a molder 20 percent. If they have eight machines, they can unplug one of them and retain the same level of productivity with the vacuum-brazed, conformally cooled mold," says Hepler.
Nearly 75 percent of Polyshot's conformal cooling fusion business involves caps and closures, says Hepler. Although Polyshot has fused conformal cooling lines into inserts that are as close as 1mm distance from the surface of the tool, a range from 0.0625 to 0.25 inch is more common.
Hepler says the flow diameters of the conformal channel can be made small; however, contaminants can clog the water line if the pathways are designed too small. H-13, P-20, 420 stainless or S7 steel that is 0.75-inch thick is preferred by Polyshot for vacuum brazing.
LARGE DMLS TOOLING PROVIDER
Linear Mold & Engineering, the largest privately held supplier of molds and inserts produced by additive manufacturing in the U.S., is expanding capacity. In the last year Linear Mold purchased an EOSINT M280 direct metal laser sintering system, and an SLM 280 selective laser melting system from SLM Solutions GmbH, Lübeck, Germany. The company has eight EOS systems and three SLM systems currently, with plans to install a total of 32 DMLS units by the end of 2015, says Young.
"Four years ago we had done just a handful of conformal cooling projects for Tier 1 and Tier 2 suppliers to the automotive industry, and one or two projects for consumer products," says Young. "Today Linear Mold supports tens of dozens of project applications for single-face, multi-cavity and stack tools, across a range of markets."
All of the DMLS tooling inserts developed by Linear Mold incorporate conformal cooling channels. Tooling inserts for plastic part production represent half of Linear Mold's business with the additive manufacturing technology; Linear Mold uses DMLS as well as selective laser sintering and fused deposition molding to produce a range of prototype and production metalized parts for the aerospace and oil and gas industries.
The DMLS process from EOS builds parts in thin layers by sintering a metal powder using a laser to trace a path from a CAD model. EOS has developed the proprietary steel-based powders for tooling.
A bed of the proprietary metal powder is spread uniformly over the build surface, with select areas sintered by a laser that follows a pattern derived from a 2-D slice of the CAD model. The building platform is lowered, another bed of metal powder is applied, and the next sliver of the CAD model directs the path of the laser. The EOS unit produces layers down to 40 microns and is accurate within 0.05mm.
Mikell Knights, senior correspondent
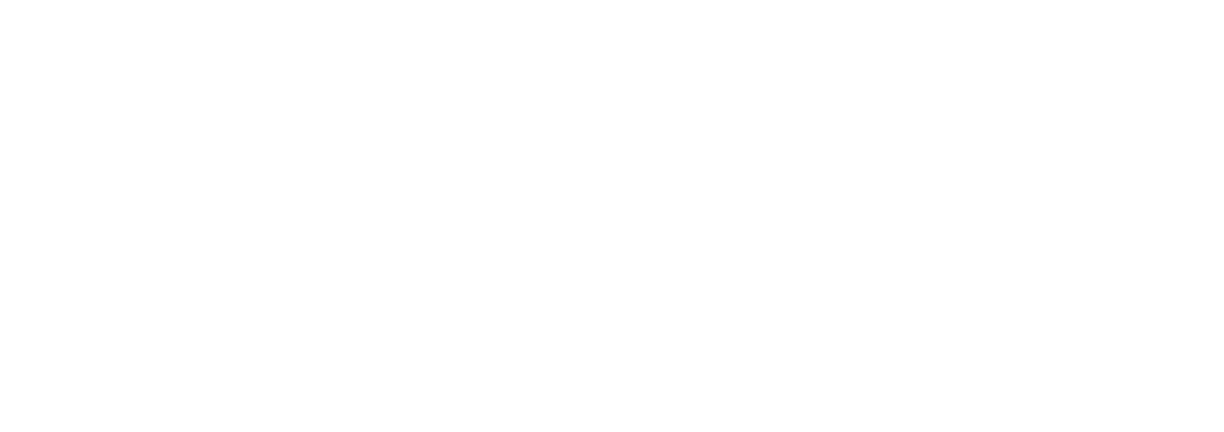