A new blow molding and filling manufacturing technology that uses the consumable liquid going into the preform as the agent to form the rigid plastic container, rather than compressed air, is being licensed to the equipment industry through LiquiForm Group, a joint venture formed between Amcor Rigid Plastics, Ann Arbor, Mich., and Sidel Group of Switzerland with offices in Norcross, Ga., United States.
The LiquiForm technology combines bottle forming and filling in a single step by pressurizing the consumable liquid that fills the preform to form the rigid container. Using pressurized, incompressible liquid in this novel combined forming and filling step eliminates the use of compressed air and the need to handle empty bottles before filling, simplifying the manufacturing process.
"With LiquiForming the bottle cools faster than in blow molding, conduction is faster than convection. The consumable doesn't taste like plastic for the same reasons that an air-blown bottle doesn't (transfer a taste to the product)," says Ann O'Hara, president of LiquiForm Group. The company has conducted numerous trials and testing across a focused range of products. Any resin used in food contact has to meet stringent FDA requirements. End users need to own the knowledge of their product and its compatibility with its package, says O'Hara.
The process starts with an optimized injection molded preform that is conditioned in an oven prior to entering a LiquiForm-capable machine to achieve defined temperature profiles. The preform is placed into the mold, then the actual consumable liquid product is forced at high pressure into the preform, molding the plastic into the bottle shape. This results in a filled bottle that is ready for capping and labeling. The consumable liquid is pressurized in one of several ways — including hydraulics — with container forming occurring under a tailored pressure profile. It reaches a peak pressure of between 20 to 40 bar, similar to current air blowing profiles and pressures. However the use of the incompressible liquid takes far less energy to reach a desired pressure compared to compressed air, says O'Hara. This approach reduces the non-resin operating costs up to 25 percent compared to traditional air blow molding and separate filling, with much of those savings derived in energy savings by eliminating compressed air. Blow pins and certain other components and their related maintenance requirements are eliminated.
Beyond the primary energy savings benefit, the use of the pressurized liquid may yield finer bottle definition than blow molding. It may also yield a higher degree of bottle filling accuracy which may allow users of the technology to tighten target fill volume or weight, reducing bottle overfilling, says O'Hara.
The concept has been under development across the LiquiForm Group partners since the mid-2000s, during which time a wide range of packaging substrates, products and conditions have been validated. The LiquiForm Group is developing the technology for all hot or cold fill applications and a range of non-beverage applications such as food products, vegetable oils, lubricants, health-care and personal-care products.
Amcor's Rigid Packaging business group and Sidel each own a 50 percent stake in the LiquiForm Group, the joint venture company, based in Switzerland as the legal entity that owns the patents and intellectual property relating to the LiquiForm technology. Yoshino Kogyosho Co., Japan's largest plastic bottle manufacturer, and Nestlé Waters North America, the world's largest bottled water company, have signed on as partners. LiquiForm has research and development at all of its partners' sites and a technical center in Saline, Mich.
LiquiForm Group will issue developmental and production licenses to equipment makers who will build and supply their own machines using the LiquiForm technology inside. And the LiquiForm Group will also work with end users / brand owners to perform product development. The degree of specialization of the equipment focuses on the product and its conditions for filling and other requirements, but the overall framework of the LiquiForm technology will be embedded in conventional equipment.
There are currently six operational prototype machines at the owner and partner companies and each one is unique and tests different approaches to the pressure mechanisms, preform making, resin characterization and other product and process perimeters. LiquiForm Group aims to offer many different choices on the technology components. Developer kits will be available in the next 6-12 months. The first commercial application of LiquiForm is expected to come on line in two to three years, says O'Hara.
So far, the technology has successfully filled cold, ambient and hot-fill PET containers as well as HDPE and PP bottles. Other resin types, including recycled and biodegradable materials, are expected to be compatible with the process. The technology will eventually be applicable to most types of blow molding machines, including injection-stretch and extrusion. Initial testing was conducted on traditional injection preform machines with form-filling testing done on modified blow molding equipment. The technology will be applicable to single- and multi-cavity tools.
Shear testing with LiquiForm was conducted through several university projects to get a sense if pressure and shear affected the consumable liquid. Testing concluded that the process did not impact any of the many products evaluated. However, interested parties will evaluate their own product and conclude if they have the correct attributes and compatibility with the process. Downstream capping and labeling steps may at some point be integrated into the LiquiForm process, says O'Hara.
Mikell Knights, senior correspondent
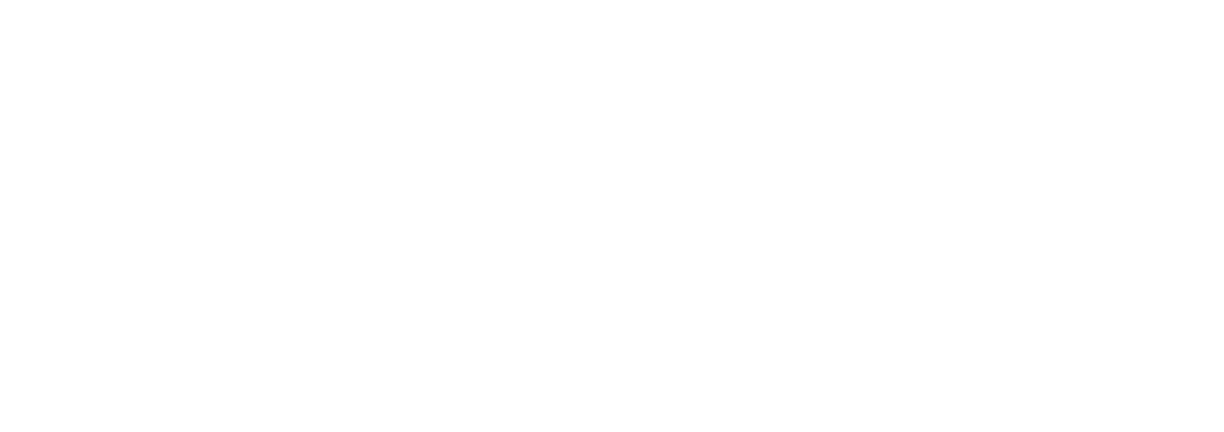