Blow molding units moving from hydraulics to hybrids, all-electrics
Suppliers of extrusion blow molding units, injection stretch blow models, shuttle designs and wheels continue to develop machines that move away from all-hydraulic designs. New market entries in hybrid designs deliver the best of both worlds, including the power of a hydraulic for faster mold transport or rapid clamp up, with servomotors that make machines programmable and processes reproducible. Meanwhile, all-electric machines target high-value applications where clean room operation is a critical criterion.
Molders should expect all-electric models to remain priced at least 10 percent higher than a similar-sized all-hydraulic, while hybrid prices are in the same ballpark as full hydraulic machines but deliver energy savings with more capabilities.
Here are a few of the most recent introductions and business developments.
EXPANDING ELECTRIC EXTRUSION BLOW
Bekum America Corp., Williamston, Mich., has expanded its 07 series of tie-bar-less, C-frame shuttle machines with the Hyblow, a new hybrid design developed in the U.S. in 2013. The first 07 series configuration debuted in 2007 with Bekum's introduction of the Eblow electric blow molding line, says Gary Carr, Bekum's North American director of sales.
The Hyblow is a lower-cost version of the Eblow that initially is only being offered as a double-sided shuttle unit. Just like Eblow, the Hyblow handles mold widths from 350mm to 700mm, delivers clamping forces from 10 to 24 metric tons and targets agricultural containers, laundry care products and automotive supplies. And, both lines are offered in a 307, 407, 507 and 607 model sizes.
Hyblow, however, features two closed-loop servo-hydraulic circuits, one governing carriage movement, the other driving clamping motions. The C-frame clamp design delivers high force distribution as well as clamp lockup speeds as fast as 200 milliseconds or less. The clamp design separates mold guidance (platens move on rails) from force containment.
Eblow clamp-up is achieved with hydrostatic transmission rather than a toggle or linkage device. A servo-electric drive powers the cam-driven movement of the carriage. Uniform force distribution and quick clamp tonnage make Eblow and Hyblow models in the 07 series suited to processing hard-to-trim materials such as PP or extrudable PET.
Compared with a Hyblow, Bekum says the Eblow gives 25 percent greater energy savings but the Eblow is priced higher as it incorporates electric servo drives and actuators on all seven distinctive machine movements of the double shuttle — including mold open and close, carriage shuttle movement and calibration for each shuttling mold, and parison programming. (Bekum based energy consumption calculations on a benchmark of 0.4 kilowatt per kilogram processed per hour.)
Bekum will eventually offer Hyblow in a single-shuttle format, and also plans to develop a version of Eblow for the U.S. market that features domestically sourced servo electric drives/motors and related components. Both Eblow and Hyblow lines are produced at Bekum's world headquarters in Germany. The company has a number of Hyblow machines in the field and under construction. Four Hyblow 607D units will be installed, and in full production, by year's end, with three more machines being shipped early next year, Carr says.
ALL-ELECTRIC KBB
Kautex Maschinenbau GmbH, Bonn, Germany, advanced its extrusion blow molding machines for packaging with the KBB all-electric press, launched a year ago. The largest of four models — the KBB80 — became available earlier this year; the KBB can produce bottles up to 10 liters while curbing energy consumption up to 42 percent, Kautex says
In the KBB80, operating, transport, and mold open and close movements have been accelerated, and traversing time from the head to the calibration position takes 0.6 second. The unit has a dry cycle time of 2.6 seconds. It can handle molds up to 960mm by 380mm and with up to 55 cavities and mold halves up to 660 pounds.
It provides shuttle stroke of 970mm, clamp stroke of 250mm and blow-pin stroke up to 100mm. The KBB series can move from monolayer to three-layer products through a simple retrofit, and is designed for 15-minute mold changeovers requiring just two people. Upgraded controls allow material and machine settings to be adjusted during production.
The compact KBB saves space by integrating leak testing and switch cabinets, and energy by using lighter materials and recovering energy expended in the braking of servomotors, according to Kautex.
"Customers can manufacture product faster because an electric motor, unlike hydraulics, doesn't need to warm up or calibrate. It's the same, first cycle to last cycle," says Chuck Flammer, vice president of sales with Kautex Machines Inc.
Though no KBB80s have been sold yet in North America, Kautex has sold a KBB60D in North America, and has sold that model in Germany as well, to Greiner Packaging and Siepe Packaging, says Flammer. Only double-station versions are being offered right now, for higher output applications.
The next upgrade for the KBB will be a next-generation of Kautex's BC software that will permit further analysis of operating parameters and more responsive controls. Two clamps can be changed out, for producing smaller lightweight bottles or larger, heavier bottles.
A virtual training tool lets operators train on the machine, via a 3-D image projection, while it's in production. Users simulate a range of functions including tool setup and machine startup, and can simulate fault conditions, like a bad parison. Production programs can also be brought into the simulation.
At NPE next year in Orlando, Fla., Kautex plans to exhibit a Meccanoplastica blow molding machine, since becoming a North American sales and service rep for Meccanoplastica Srl's series of Jet electric injection blow machines and it MIPET stretch blow machines, for PET. Flammer says there will be no cross technology between the companies.
CHARGING ISBM
An injection stretch blow molding machine with a hybrid power source is Nissei ASB Co.'s newest roll-out for the high mix, low production of small bottles and jars up to 2.5 liters and with a 70mm neck diameter. Two servomotors drive hydraulic pumps for transporting, stretching and blowing actions of the ASB-12M, introduced last year.
The one-step ISBM ASB-12M is small enough for a lab testing machine or for producing small runs, for example pharmaceutical bottles running eight-up at 3,300 an hour. At Japan's recent International Plastics Fair, an ASB-12M produced 100-milliliter PET cosmetic jars weighing 60 grams apiece, with a thick base and 59mm neck, at 170 containers per hour. The new one-step unit joins the ASB-15N/10E all-electric ISBM model, which has nine servomotors and is suited for clean room and high-value-added bottle applications. Jamie Pace, VP & GM, ASB, says 10 units are being used commercially in Asia.
Nissei ASB, Atlanta, has plans to transfer the hybrid servomotor/hydraulic circuit concept to other ASB models that rely on variable hydraulic pumps for drive. The ASB-70DPH (V4) model, designed for bottles from 5 milliliters to 10 liters, debuted last month at IPF with a hybrid servo-hydraulic system rather than a displacement pump with a larger hydraulic oil reservoir. The model, also equipped with a unique conditioning station, produced 42-gram PET warm-fill bottles with 500-milliliter of capacity and a 32mm neck at 1,350 bottles per hour. Energy savings and less maintenance come from the servo's ability to stop hydraulic oil flow when the machine isn't moving, unlike fixed or variable pumps where rotation is maintained and power required at all times.
Another recent hybrid servo-hydraulic drive design from ASB is the PF24-8B, a 1.5-step PET injection stretch blow machine, for making bottles from 500 milliliters to 5 liters at rates up to 9,000 bottles an hour. The machine produces the PET preform, which is partially cooled, temperature equalized, reheated with quartz lamps and blown in a cool parison system. Using a compact injection clamp with fewer blow molds provides performance output with lower mold costs. ASB has installed 30 PF24-8B machines, the majority in Asia.
REHEAT STRETCH BLOW
The new Sidel SBO Matrix reheat stretch blow molding units from Sidel Inc., Norcross, Ga., produce lightweight PET bottles from up to 3.5 liters at rates up to 2,250 bottles per cavity depending on bottle size. Launched in 2013, the Matrix is said to trim oven electrical consumption up to 45 percent and air consumption up to 35 percent compared to the SBO Universal series, through a combination of enhancements, including new oven technology and a novel "double air recycling" approach said to reduce the air consumption of the system. Matrix is offered in an XS version to produce up to 0.75 liter bottles, an M version with a larger clamp for larger bottles up to 2 liters, and an L version that generates bottles up to 3.5 liters.
Matrix is the replacement for Sidel's SBO Universal2 line of reheat stretch-blow molding units. One key difference between Matrix and SBO Universal is a change in the actuation of the stretching function. The stretching function, executed on the Universal series with a pneumatic cylinder and fixed cam, is updated with the implementation of linear motors that replace the pneumatic cylinder. The shift to linear motor stretch rod actuation makes the stroke action electric and programmable. The ability to program the stroke length of the stretch rod permits a larger range of bottle shapes to be molded without having to change out complex components. It also eliminates the need for air and no greasing is required.
Matrix also reconfigured a measurement technology that ensures bottle quality as molders produce lighter-weight bottles faster. Sidel's new Intelli-blower system uses internal information from the reheat stretch blow machine blowing profile, adjusting various blowing parameters to maintain a consistent blowing curve, which Sidel says provides an indication of consistent process and consistent bottle quality.
The previous Universal series machine used external sensors to create a closed-loop machine control response based around a bottle weight measurement. However a dirty or otherwise impacted sensor could detect a false reading and change process parameters.
The Matrix system adjusts machinery parameters based on the variation from a set reference point that is established during the setup process. Conditions relating to the blowing curve and other machine conditions that reflect ideal bottle production are captured by the Intelli-blower. The reference point is used to adjust the blowing profile for each station. The system can adjust parameters automatically or alert an operator. The new PLC makes it possible to run the new Intelli-blower system on Matrix.
WHEEL DEVELOPMENTS
Graham Engineering Corp., York, Pa., which makes extrusion blow molding machines in rotary wheel, accumulator head, shuttle and shot pot designs, developed two new capabilities to make its G series wheel line more flexible, increase efficiency and produce a wider range of bottles.
A new variable pitch design for its continuous extrusion rotary wheel G series allows users to change the pitch radius of a mold station from one radius to another in five to 10 minutes per station. That ability permits the molding of multiple bottle sizes on one system. Introduced in 2013, the variable pitch capability connects each mold station onto redesigned hubs that quickly connect and disconnect to the machine, allowing for faster changeovers.
Historically, wheel machine molding stations were supported by hubs integral to the clamp with a fixed clamp centerline, or pitch radius. As a result, users were limited in the size range of containers and the ability to control scrap. The variable pitch design makes it possible for a molder to change the pitch radius of all the stations in a wheel machine over the course of a single production shift.
Graham also developed a new modular clamp design for the G series that facilitates fast mold changeovers and allows molders to add or subtract clamp stations. The G series relies on a variable frequency drive to control the machine's cam-actuated motions, such as opening and closing the mold.
Graham expanded its plastic extrusion machinery platform by acquiring Welex Inc. in 2013 and American Kuhne in 2012, and integrated those brands. Graham's Pennsylvania headquarters, the hub for system, line, control and integration expertise, is where Graham blow molding machinery is produced.
Mikell Knights, senior correspondent
Related article: Kautex assesses real machines in virtual world
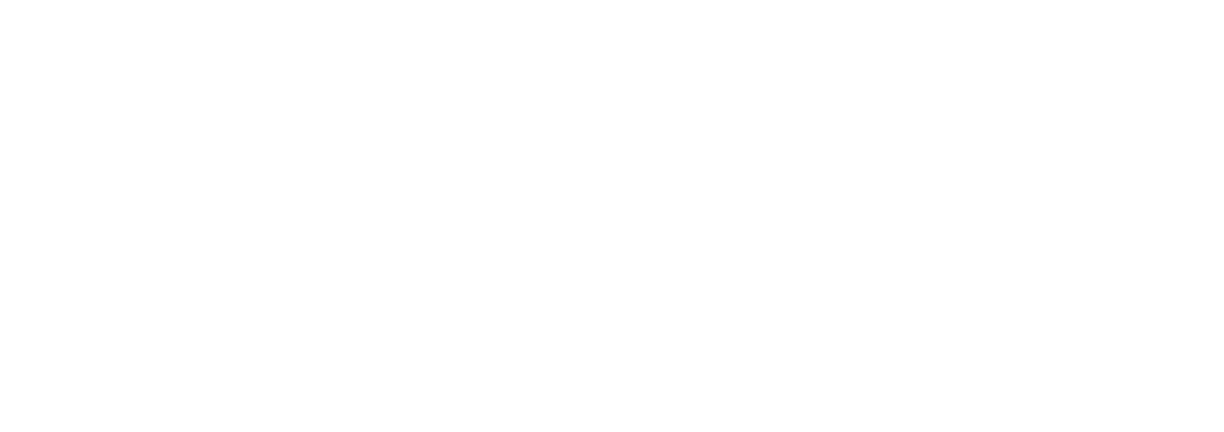