Makers of resin-drying equipment are constantly improving their technology to ensure the best possible material performance. Several manufacturers recently have upgraded control units and unveiled new desiccant dryer models, including ones targeted at medical applications and hygroscopic resins.
MORETTO SPA
At the K show, Moretto SpA, Massanzago, Italy, introduced its X-Comb dryer, which it developed to meet the needs of the medical industry.
"The X-Comb dryer brings together some of our most innovative technologies," Benjamin Sutch, chief marketing officer, said. "We engineered this dryer to be medical-ready, Industry 4.0-compliant, and all the while optimizing energy consumption for small-batch and engineering resins."
The X-Comb dryer can be mounted on or beside an injection molding machine and features Moretto's OTX hopper, which has a specialized internal geometry to improve material mass flow and air distribution. It has an integrated touch-screen control and is available in four sizes, with throughputs ranging from 3.1 to 32 pounds per hour.
Its dew-point equalizer manages the speed and revolution of a zeolite-based desiccant cartridge, allowing the dryer to achieve a stable dew point of minus 61.6 degrees Fahrenheit.
One of the main benefits of the new unit is efficiency, Sutch said. The OTX hopper requires 40 percent less drying time and airflow, and a lower hopper volume to treat the same amount of resin as a conventional hopper. Together, the X-Comb's self-adjusting variable airflow and resin anti-stress control ensure optimal drying without over-drying. Also, no tools are needed to access the filter for cleaning and replacement.
An integrated color touch-screen control comes standard. The interface allows for quick selection and control of all dryer parameters. The control also can manage an optional feeder that can be purchased along with the dryer.
DRI-AIR INDUSTRIES INC.
Dri-Air Industries Inc., East Windsor, Conn., recently added the 1500 FM to its line of large desiccant dryers.
The 1500 FM is a floor-mounted model based on Dri-Air's 750 FM design. With its larger towers and blowers, it's for use with central drying systems and extruders that have outputs of as much as 1,500 pounds per hour. It has a compact footprint of 30 square feet.
A new regeneration airflow design for the 1500 FM reduces energy consumption by 25 percent compared to previous levels for FM models. Dry air, rather than ambient air, is used for regeneration or cool down of desiccant towers, allowing for dew points of minus 80 degrees Fahrenheit or lower. A unique regeneration valve is easily accessible for quick troubleshooting without the need to remove dryer panels. All external panels are hinged for quick access to internal components, but they can be slipped off their hinges when working in confined spaces.
A high-pressure fan operates at noise levels of less than 70 decibels, and the fan allows the dryer to operate at very low process temperatures to accommodate resins including polylactid acid, according to the company.
The 1500 FM features the company's Dri-Touch controls, which display important operating parameters on a highly visible 7-inch touch screen. The menu screen provides access to all settings and other parameters needed during setup and troubleshooting.
Dri-Air Industries also has developed an algorithm for the regeneration sequence on all large dryers. The algorithm fine-tunes heater cycles for high-performance four-bed dryers, resulting in additional energy savings and better performance, compared to earlier models. With this algorithm, the dryer uses only 40 percent of the energy of a typical desiccant-wheel dryer, company President Charles Sears said.
The company has made the feature standard on all large dryers and is in the process of adding it to Dri-Air's entire line of dryers.
LABOTEK A/S
Labotek A/S, Frederikssund, Denmark, is introducing its new DMR (Desiccant Mobile Rotor) series of resin dryers to the U.S. market. They will be available by the end of the first quarter through Romax Inc., Hudson, Mass.
"The DRM dryer is a wheel-type desiccant dryer system that is applicable to low- and medium-usage requirements and is portable," Eric Roberts, Romax's director of sales and marketing, said.
The dryers are available in three sizes, with capacities of 40 liters, 75 liters and 110 liters.
The compact dryers can achieve dew points of minus 40 degrees Fahrenheit or lower, according to the company. They offer a footprint of only 6.5 square feet. The heavy insulated drying hopper is made of stainless steel.
A Siemens PLC comes standard, as does a three-year warranty.
Optional features include conveying units to and from the DMR dryer and a built-in dew-point sensor.
MOTAN INC.
Motan Inc., Plainwell, Mich., recently introduced a new range of small, mobile dryers for use with hygroscopic resins.
The new Luxor E A and Luxor EM A models use desiccant drying technology and offer drying bins with volumes of 2.1, 3.5 and 5.3 cubic feet.
"These are high-quality dryers offering all the advanced features that are included in our larger centralized drying stations," said Carl Litherland, head of group marketing.
The Luxor E A models are designed to be integrated into existing raw materials conveying systems or, alternatively, they can be equipped with their own stand-alone loader.
The Luxor EM A dryers come with an integrated conveying system and are self-contained mobile units. They are equipped with a side channel blower, as well as a cyclone dust collection filter with an easy-to-clean cartridge and transparent dust-collection bin. The pipework for dry-air conveying features rigid hose connections and ensures that the suction box is protected from ambient air, and that dry air always is used for conveying. The closed system allows material to remain in the suction box even during down times, so the resin continues to be protected from moisture in a dry environment.
Both lines of dryers use a closed process cycle in conjunction with temperature-controlled regeneration of the desiccant bed. The closed-cycle drying process means dryers can produce process air with very low dew points even when operating in humid environments.
The dryers are operated using the new Luxornet EM control, which offers user-friendly operation through a color graphic display with a touch screen. The touch-screen controls process functions and recipes, and produces quality-assurance and service-function information, as well as trend charts.
Available as an option, the dryers' ETA plus technology automatically adapts airflow and drying temperature to the material throughput for energy savings of as much as 64 percent compared to conventional drying systems.
Bruce Geiselman, senior staff reporter
Contact:
Dri-Air Industries Inc., 860-627-5110, www.dri-air.com
Moretto USA LLC, 614-541-9696, www.moretto.com
Motan Inc., 269-685-1050, www.motan-colortonic.com
Romax Inc., 502-327-8555, www.romaxinc.com
Bruce Geiselman
Senior Staff Reporter Bruce Geiselman covers extrusion, blow molding, additive manufacturing, automation and end markets including automotive and packaging. He also writes features, including In Other Words and Problem Solved, for Plastics Machinery & Manufacturing, Plastics Recycling and The Journal of Blow Molding. He has extensive experience in daily and magazine journalism.
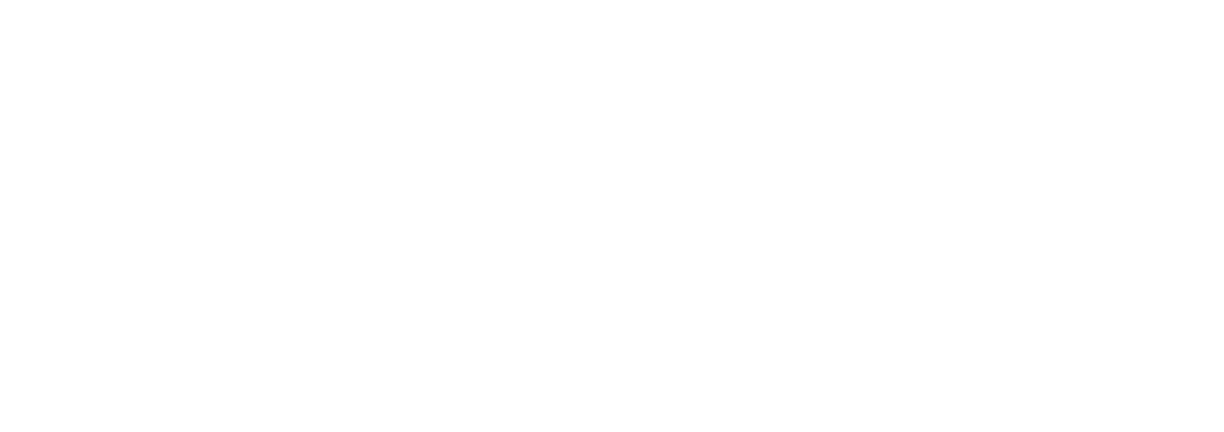